Table of Contents
ToggleLiquid Silicone Rubber (LSR) is one of the most versatile and durable materials used across a wide range of industries. Including automotive, medical, electronics, consumer goods, and more. Known for its high-performance qualities, LSR is increasingly becoming a go-to material for manufacturers worldwide.
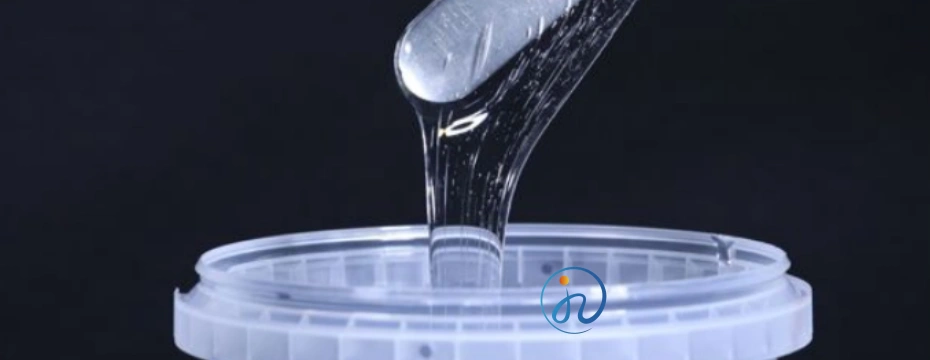
But what does the future hold for Liquid Silicone Rubber? This article explores the emerging trends, innovations, and market opportunities. They are shaping the future of LSR, with a particular focus on its expanding applications and technological advancements.
1. Overview of Liquid Silicone Rubber (LSR)
Liquid Silicone Rubber (LSR) is a two-component material made from silicon, which is then injected into a mold to create parts. It is distinct from solid silicone due to its fluid consistency before curing. LSR is known for its:
- Durability: LSR is heat-resistant, chemical-resistant, and offers excellent weathering properties.
- Flexibility: It has excellent stretch properties, making it ideal for applications requiring flexibility.
- Biocompatibility: LSR is widely used in medical devices, as it is non-toxic and biocompatible.
- Moldability: LSR is easy to mold into complex shapes with high precision, making it perfect for intricate designs.
These properties have contributed to the growing popularity of LSR, especially in industries where performance and precision are critical.
2. Key Trends Shaping the Future of LSR
2.1 Increased Demand in the Medical Industry
The demand for LSR in medical applications is poised to grow significantly due to its excellent biocompatibility, sterilizability, and ability to be molded into highly precise shapes. With a rise in minimally invasive surgeries, wearable medical devices, and implants, the need for LSR in the healthcare industry is expanding.
- Wearable Health Devices: LSR is used in wearable devices like fitness trackers and medical monitoring systems due to its durability and flexibility. These devices require materials that can withstand exposure to sweat, moisture, and temperature fluctuations, all of which LSR offers.
- Surgical and Implantable Devices: LSR’s ability to withstand sterilization and its non-reactivity with human tissues make it ideal for surgical components, including gaskets, seals, and prosthetics.
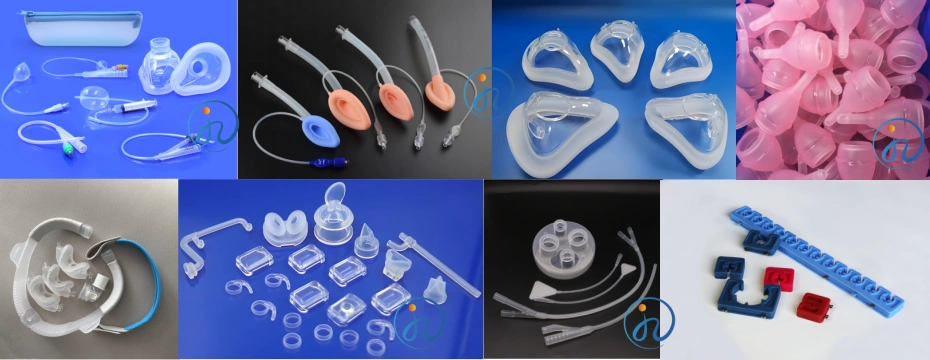
2.2 Growth in Automotive Applications
LSR’s unique combination of durability, high-temperature resistance, and flexibility has made it indispensable in the automotive industry. It is used in the production of gaskets, seals, and components that need to withstand harsh conditions, including extreme temperatures and exposure to chemicals.
- Electric Vehicles (EVs): With the rise of electric vehicles, LSR’s use in seals and gaskets for batteries, electrical systems, and connectors is expecting to grow. As EVs require materials that offer high-performance sealing and insulation properties, LSR’s role in this sector will become even more prominent.
- Fuel Efficiency and Environmental Regulations: As the automotive industry faces stricter environmental regulations, manufacturers are turning to LSR to improve fuel efficiency and reduce emissions by using advanced sealing technologies.
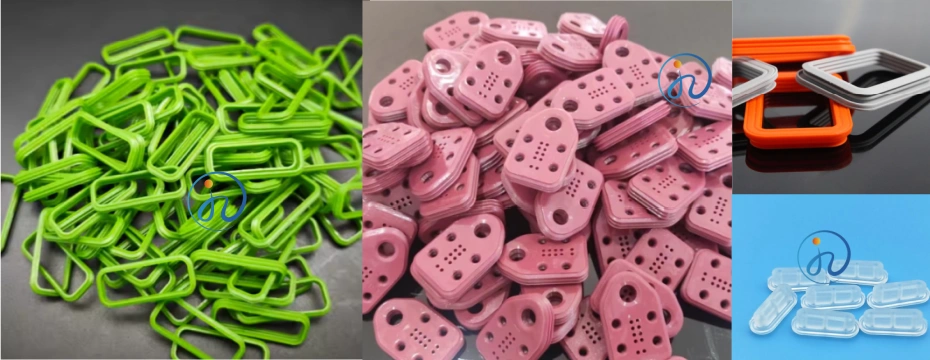
2.3 Advancements in 3D Printing with LSR
3D printing, or additive manufacturing, is revolutionizing the way industries create prototypes and parts. LSR is starting to play a critical role in this process as 3D printing technologies improve.
- Customization and Prototyping: Manufacturers can create highly customized parts quickly, which is essential for industries like healthcare, automotive, and aerospace.
- Faster Production Cycles: 3D printing with LSR enables rapid prototyping and low-volume production with shorter lead times, thus providing greater flexibility and reducing costs.
2.4 Sustainability and Recycling Initiatives
As sustainability becomes a top priority for businesses globally, the focus is shifting toward more eco-friendly production methods and materials. In response to growing environmental concerns, LSR is evolving to meet sustainability standards.
- Biodegradable and Recyclable LSR: Manufacturers are exploring options for biodegradable and recyclable LSR formulations, enabling the material to be more eco-friendly throughout its lifecycle.
- Energy-Efficient Manufacturing: Advances in LSR manufacturing technologies, such as energy-efficient injection molding machines, are reducing the environmental impact of production processes.
3. Innovations in LSR Technology
3.1 Improved Cure Systems
Traditionally, LSR requires heat to cure in the mold, but new advancements in curing systems are making the process more energy-efficient and faster. For instance:
- UV-Curing LSR: UV-cured LSR offers faster curing times, which can improve productivity and reduce energy consumption.
- Low-Temperature Curing: Research into low-temperature LSR curing could lead to more energy-efficient manufacturing processes and expanded use in applications that require lower processing temperatures.
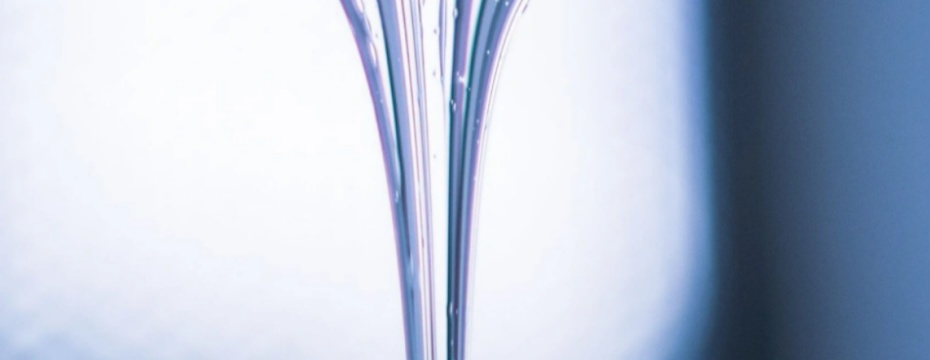
3.2 Hybrid LSR Compositions
The development of hybrid LSR compositions is enhancing the material’s performance. These new blends of LSR with other polymers or materials offer improved properties such as enhanced strength, conductivity, or thermal resistance.
- Conductive LSR: Conductive LSR is making its way into electronics, where it can be using for custom connectors, switches, and conductive gaskets.
- Reinforced LSR: Reinforced LSR materials, made with added fibers or fillers, provide additional strength and performance in high-stress applications, such as in automotive and aerospace industries.
3.3 Smart LSR Materials
The development of smart LSR materials, which can respond to environmental stimuli (such as temperature, light, or pressure), is one of the most exciting innovations in the field. These materials can be integrating into various products, including sensors, actuators, and other IoT devices.
- Self-Healing LSR: Self-healing LSR could lead to longer product lifespans by enabling the material to repair minor damages autonomously.
- Shape Memory LSR: Shape memory LSR could allow parts to return to their original shape after being deforming, opening new possibilities for applications in robotics and medical devices.
4. Market Growth and Future Opportunities
The future of Liquid Silicone Rubber looks promising, with expanding applications in high-growth industries. Market research suggests that the global LSR market is expecting to grow at a significant rate, driven by demand in key sectors like healthcare, automotive, and consumer goods.
4.1 Emerging Markets
- Asia-Pacific: Countries like China, Japan, and India are experiencing rapid industrialization and are expecting to become major consumers of LSR in automotive, electronics, and medical device manufacturing.
- Latin America and Africa: While the LSR market is more mature in North America and Europe, emerging economies in Latin America and Africa present untapped opportunities, especially in consumer products and automotive sectors.
4.2 Diversification into New Applications
While LSR is already using extensively in traditional industries, new applications are emerging in fields like:
- Robotics: Flexible, durable silicone parts are increasingly being used in robots and other automated systems.
- Aerospace: LSR’s resistance to extreme temperatures and harsh conditions makes it an attractive material for aerospace applications, particularly in seals and gaskets.
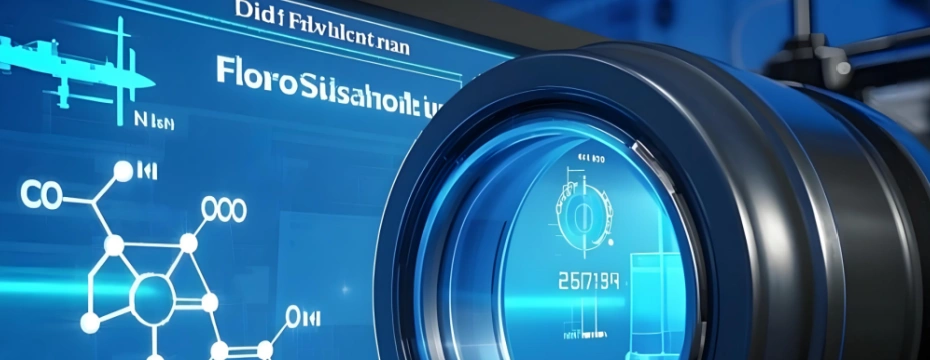
5. Challenges in the LSR Industry
Despite its many advantages, the LSR industry faces several challenges that could impact its future growth:
- Cost of Production: LSR can be expensive to produce, particularly when it comes to high-performance grades. However, innovations in manufacturing and material optimization could help drive down costs.
- Supply Chain Issues: As with many industries, supply chain disruptions can affect the availability of raw materials and components, potentially slowing down production timelines.
Conclusion
The future of Liquid Silicone Rubber (LSR) is bright, with numerous opportunities across various industries. As demand for high-performance materials continues to rise, LSR is poising to play an even more critical role in shaping the next generation of products.
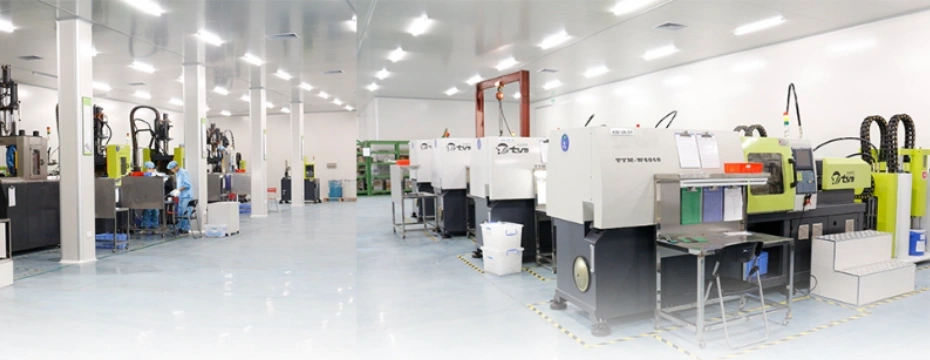
With advancements in technology, sustainability, and market expansion, LSR will remain a key material for innovative solutions in healthcare, automotive, electronics, and more. The evolving landscape of LSR promises a future full of exciting possibilities, driven by innovation, efficiency, and sustainability.