Table of Contents
ToggleLiquid Silicone Rubber (LSR) Materials Inspection: Why It Matters
Liquid Silicone Rubber (LSR) is widely used in industries that demand high precision, flexibility, and biocompatibility—such as medical, automotive, electronics, and baby products. To meet these high standards, LSR materials inspection is critical during both raw material qualification and final product validation.
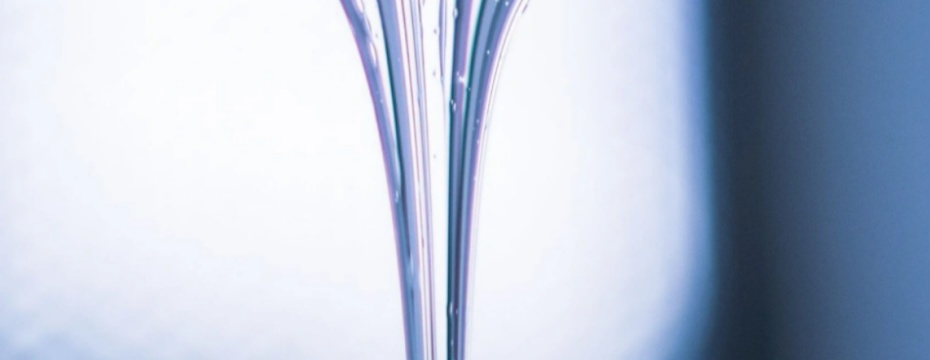
This article covers everything manufacturers and engineers need to know about LSR inspection processes—from incoming material checks to post-molding quality controls.
What Is LSR Material Inspection?
LSR material inspection refers to the process of verifying the physical, chemical, and mechanical properties of liquid silicone rubber at different stages of production. These inspections ensure that the material and finished components meet the specifications required by regulatory standards and customer expectations.
Inspections can be divided into three major stages:
- Incoming material inspection
- In-process inspection
- Final product inspection
1. Incoming LSR Material Inspection
Before production begins, raw LSR materials must be validated to confirm:
- Purity and consistency
- Mixing ratio accuracy (A/B components)
- Batch traceability
- Moisture content and viscosity
Typical test methods include:
- Viscosity test (Brookfield viscometer)
- Color consistency under controlled lighting
- FTIR spectroscopy for chemical composition analysis
- Shelf life check and lot number verification
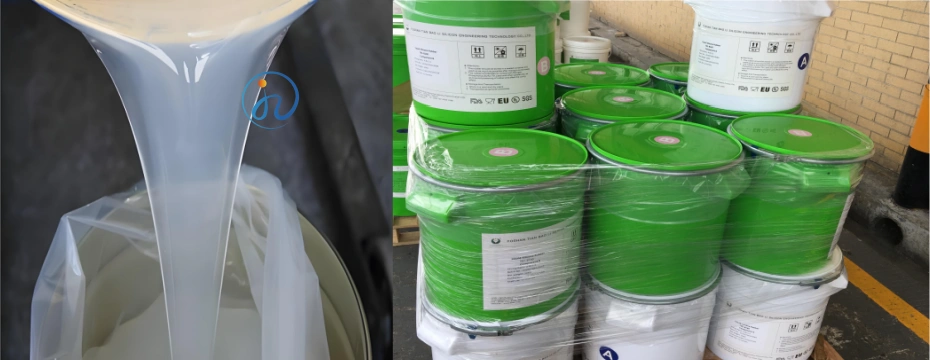
2. In-Process Inspection During LSR Molding
Once molding begins, quality control teams monitor several key indicators:
- Injection pressure and temperature consistency
- Cycle time validation
- Flash control and parting line quality
- Cure completeness (cross-linking confirmation)
Real-time monitoring systems and SPC (Statistical Process Control) tools are often used to ensure consistency and to quickly detect any deviation from standard parameters.
3. Final Product Inspection of LSR Components
After molding, finished LSR parts undergo rigorous inspection procedures to confirm:
- Dimensional accuracy (using CMM, 2D vision, or digital calipers)
- Tear and tensile strength
- Elongation and compression set
- Shore A hardness
- Surface finish (smoothness, matte, or textured)
- Visual inspection for bubbles, voids, color inconsistencies, or flash

For critical components, especially in medical devices or aerospace applications, parts may also undergo:
- Biocompatibility tests (ISO 10993)
- X-ray or ultrasonic inspection
- Microbial and sterilization validation
Key Standards for LSR Quality Control
LSR materials and molded parts must often comply with industry-specific standards. Some of the most relevant include:
- ISO 9001 – General quality management
- ISO 13485 – Medical device manufacturing
- ISO 10993 – Biocompatibility testing
- USP Class VI – Safety for biomedical use
- FDA 21 CFR 177.2600 – Food-grade compliance
- RoHS / REACH – Environmental and chemical safety
Following these standards ensures safety, product reliability, and market acceptance.
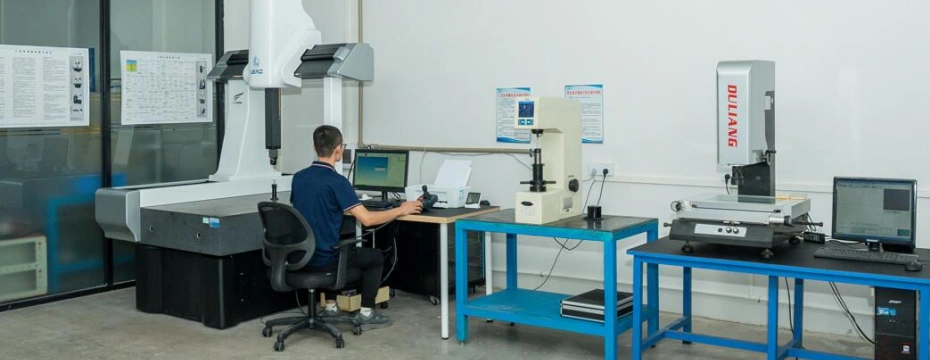
Best Practices for LSR Material Inspection
To maintain a high-quality standard, manufacturers should implement:
- Material Certification: Always source LSR from certified suppliers and request Material Safety Data Sheets (MSDS) and Certificates of Analysis (COA).
- Inspection SOPs: Define Standard Operating Procedures for each inspection phase.
- Calibration Schedule: Regularly calibrate inspection instruments.
- Document Control: Maintain traceable records for audits and client reference.
- Employee Training: Ensure operators and QC staff are training on inspection protocols.
Challenges in LSR Quality Inspection
Despite its advantages, LSR can pose unique inspection challenges:
- Low visibility of internal defects in translucent parts
- Dimensional shifts due to thermal expansion
- Deformation during handling
- Flash in micro-features or thin walls
To mitigate these, non-destructive testing and post-cure stability checks are increasingly using.
The Role of Automation in LSR Inspection
With the increasing demand for micro-molded and medical-grade LSR parts, automation is playing a bigger role in inspection:
- Automated optical inspection (AOI) for surface flaws
- Laser scanning for fast dimensional analysis
- Machine vision systems integrated into molding machines
- AI-based defect detection for real-time rejection of defective parts
These technologies significantly reduce human error and improve throughput.
Conclusion: The Value of LSR Material Inspection
Liquid Silicone Rubber (LSR) materials inspection is not just a quality control step—it’s a critical part of ensuring that the final product meets stringent industry requirements. From validating raw materials to inspecting every molded detail, consistent inspection practices reduce defects, ensure regulatory compliance, and build trust with end-users.
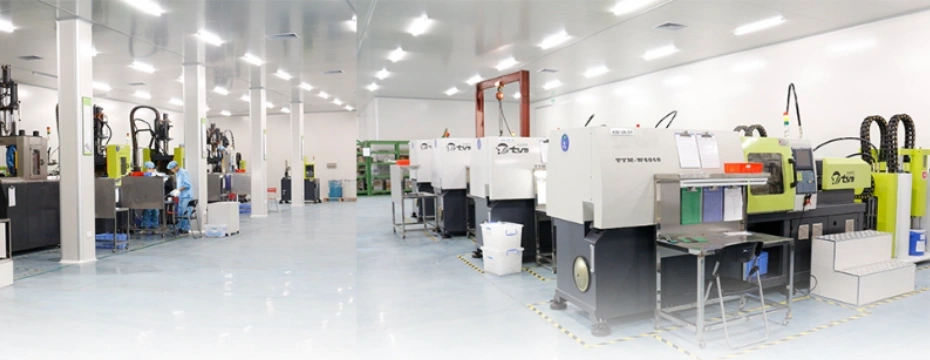
Manufacturers looking to compete globally must implement robust LSR inspection protocols backed by modern testing tools and certified processes.
FAQs About LSR Materials Inspection
Q: How often should LSR materials be inspected?
A: Incoming batches should be checked for every lot; in-process and final inspections should follow frequency defined in your quality plan or customer agreement.
Q: Can LSR parts be inspected non-destructively?
A: Yes. Techniques like X-ray, ultrasound, and optical scanning are used for critical or sealed components.
Q: What’s the most important test for medical LSR products?
A: Biocompatibility (ISO 10993) and dimensional tolerance are key. In some cases, sterilization compatibility is also crucial.