Table of Contents
ToggleIn the wake of growing global demand for reusable, comfortable, and highly effective respiratory protection, the silicone moulded half face mask respirator has emerged as a preferred choice across multiple industries. Unlike disposable masks, these respirators offer durability, flexibility, and a tight seal, making them ideal for medical, industrial, and emergency response applications.
But how exactly are these complex, high-performance masks manufactured?
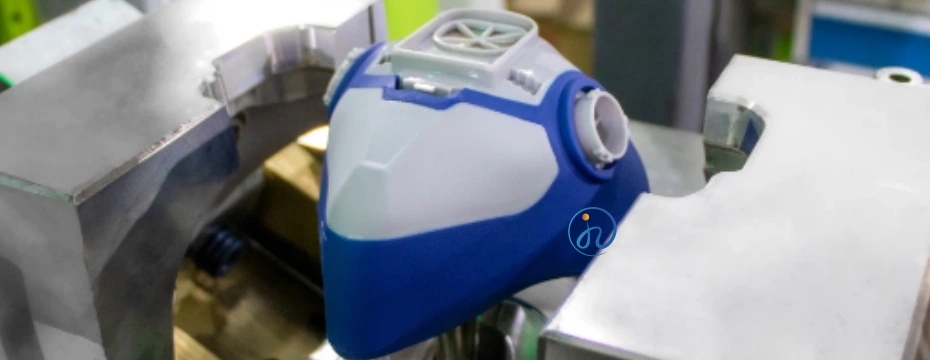
This comprehensive guide outlines the full production process of silicone moulded half face mask respirators, from raw material selection and mold design to liquid silicone rubber (LSR) injection molding and final quality inspection. Whether you’re a product engineer, PPE brand owner, or procurement manager, this article will help you understand the technologies and precision behind producing these critical safety devices.
1. Understanding the Silicone Moulded Half Face Mask Respirator
Before diving into the manufacturing steps, let’s briefly review what defines a silicone moulded half face mask respirator.
Key Features:
- Covers nose and mouth (half-face)
- Made from medical-grade liquid silicone rubber (LSR)
- Provides a flexible, airtight seal against the user’s face
- Includes filter cartridge ports and exhalation valves
- Reusable and easy to sterilize
These respirators are favored for their hypoallergenic, heat-resistant, and long-lasting properties, making them ideal for both clinical and industrial environments.
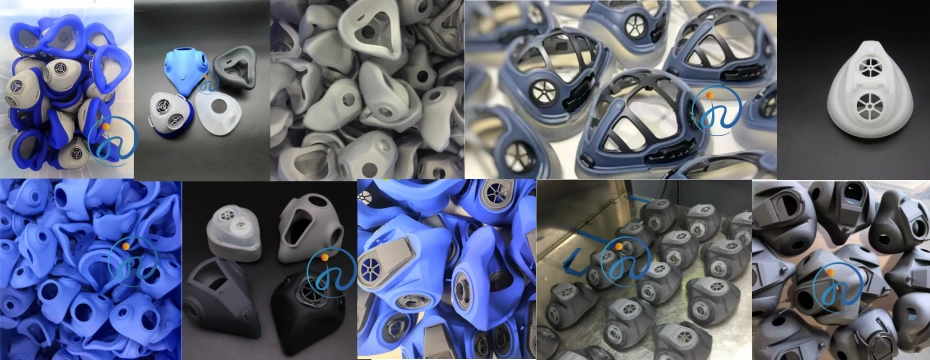
2. Material Selection: Choosing the Right Silicone
The first step in production is selecting the correct liquid silicone rubber (LSR) formulation.
Key Material Requirements:
- Biocompatibility (ISO 10993 / USP Class VI for medical use)
- High tear strength and elongation
- Low compression set for long-term sealing
- Thermal stability from -40°C to 200°C
- Colorability for branding or safety codes
Manufacturers often work with LSR suppliers to customize grades based on the product’s intended use—whether for food-grade or medical-grade respirators.
3. Mold Design and Tooling Development
Producing a high-quality silicone moulded half face mask respirator begins with precision mold engineering.
Key Considerations in Mold Design:
- Multi-cavity tooling for efficient volume production
- Complex geometries to form mask contours, valve ports, and sealing flanges
- Steel hardness selection (e.g., H13 or S136 stainless steel) for mold durability
- Ventilation and degassing systems for proper silicone flow
Computer-aided design (CAD) and mold flow simulation are typically used to optimize the mold before actual tooling begins. Precision is critical—an imperfect mold can result in poor fit or sealing failure.
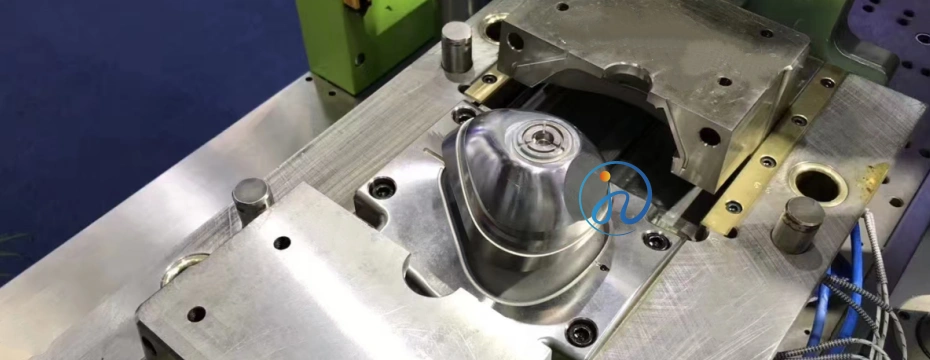
4. Liquid Silicone Rubber (LSR) Injection Molding Process
LSR injection molding is the heart of respirator production. This fully automated process ensures high consistency, low contamination risk, and tight tolerances.
Step-by-Step Process:
A. Material Feeding
- LSR A and B components are stored in sealed drums.
- A metering pump system feeds equal parts into a static mixer, where additives (colorants, catalysts) are added if necessary.
B. Injection into Mold
- The mixed LSR is injected into a closed, pre-heated mold (typically 160–200°C).
- The silicone cures rapidly inside the mold under pressure.
C. Curing and Cooling
- Vulcanization takes 30–90 seconds depending on part thickness.
- The molded respirator is then ejected and transferred to a cooling tray.
D. Demolding and Trimming
- Semi-automated systems remove the part from the cavity.
- Manual or robotic trimming removes any flash or excess material.
This process results in seamless, airtight, and biocompatible respirator masks ready for further assembly.
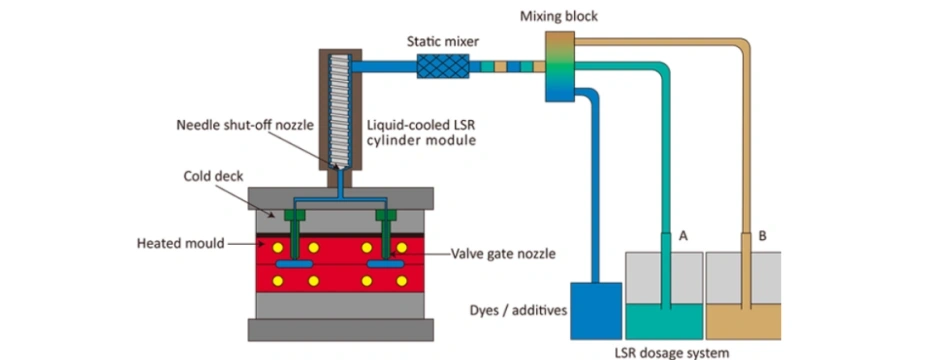
5. Assembly of Respirator Components
While the facepiece is silicone-molded, additional components are required to make a functional respirator.
Components Include:
- Inhalation/exhalation valves
- Filter cartridge adapters
- Elastic or silicone straps
- Plastic support frames (optional)
These parts are assembling manually or using semi-automated stations. Ultrasonic welding or adhesive bonding may be used for plastic-to-silicone integration.
Special attention is paid to valve seating and airtight seals, as these affect the respirator’s performance.
6. Surface Treatment and Branding (Optional)
Depending on customer requirements, respirators may undergo surface treatments such as:
- Silicone coating for a matte or textured finish
- Laser marking or pad printing for logos, sizes, or instructions
- Color coding to indicate filtration type or standard compliance
Medical-grade masks may also go through gamma sterilization or EtO sterilization, especially for hospital-ready use.
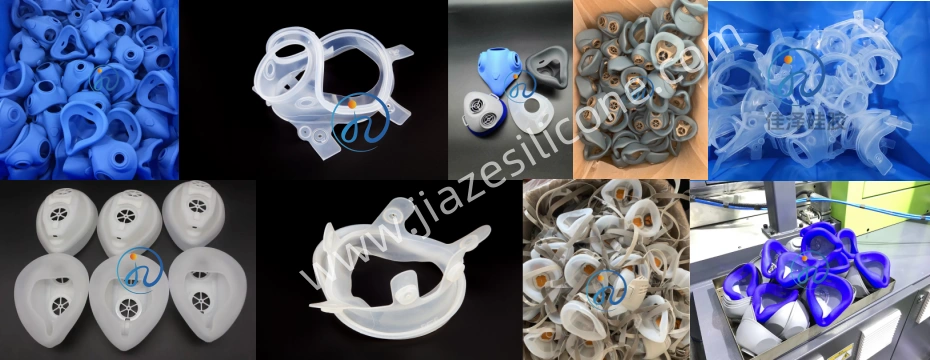
7. Quality Control and Testing
Quality is non-negotiable in respirator production, especially when lives are at stake. Each silicone moulded half face mask respirator must undergo rigorous testing.
Common Tests Include:
- Visual inspection for bubbles, flash, or discoloration
- Leak testing (negative pressure seal check)
- Tensile strength and elongation tests
- Filter port compatibility
- Fit testing (qualitative and quantitative methods)
- Biocompatibility and odor tests for medical applications
Certified manufacturers also comply with ISO 13485 or ISO 9001, ensuring traceability and documentation throughout the production process.
8. Packaging and Shipping
After passing inspection, respirators are packing according to end-use:
- Single units for consumer or healthcare markets
- Bulk packaging for industrial distribution
- Sterile barrier packaging for hospital-grade masks
Labels typically include information such as:
- Model number and size
- Manufacturing date and batch number
- Usage instructions and warnings
- Applicable standards (e.g., NIOSH, EN 140, GB2626)
9. Regulatory Compliance and Certifications
To sell or distribute silicone moulded half face mask respirators, manufacturers must meet strict regulatory standards.
Common Certifications:
- NIOSH Approval (USA)
- EN 140:1998 / EN 14387 (EU)
- GB2626-2019 (China)
- FDA Registration (if used as a medical device)
- CE Marking for European markets
These certifications verify filtration efficiency, safety, and usability, allowing the product to enter regulated markets legally.
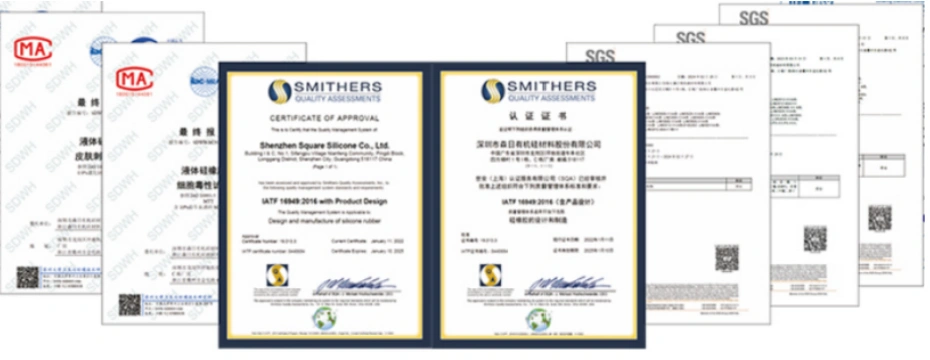
Conclusion
The production of a silicone moulded half face mask respirator is a technologically advanced and highly regulated process. From material selection and precision mold design to LSR injection molding and multi-stage quality control, every step must be executed with accuracy and care.
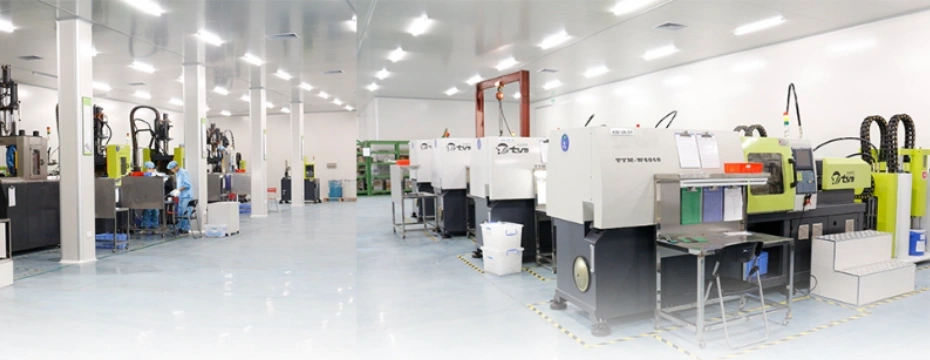
As a PPE manufacturer or OEM brand, investing in LSR molding technology offers a pathway to create durable, reusable, and high-performance respiratory masks for both industrial and medical markets. With growing demand for sustainable and safe PPE, silicone half-face respirators are not just a product of today—but of the future.