Table of Contents
ToggleThe demand for CPAP masks liquid silicone pillows continues to grow as more individuals rely on continuous positive airway pressure (CPAP) therapy to treat sleep apnea and related breathing disorders. To ensure both comfort and performance, leading manufacturers turn to liquid silicone rubber (LSR) to produce the soft nasal pillow components of CPAP masks.
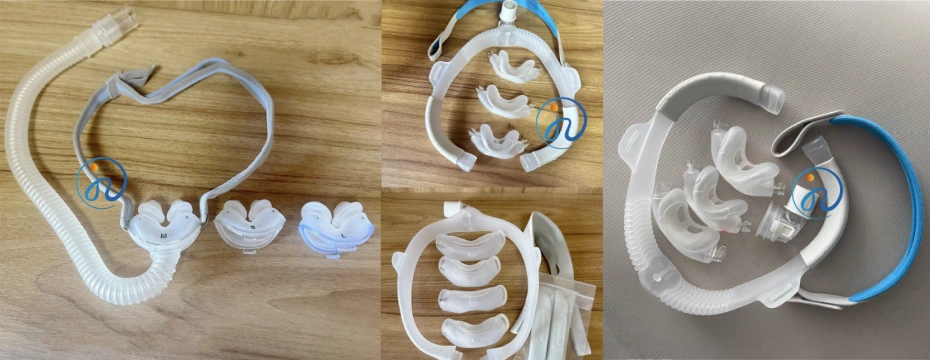
In this guide, we will walk through the entire production process of CPAP masks featuring liquid silicone pillows — from material selection to final quality inspection — to help buyers, engineers, and manufacturers understand how these critical medical devices are made.
1. Why Use Liquid Silicone Rubber (LSR) for CPAP Mask Pillows?
Comfort and Flexibility
Liquid silicone is extremely soft and skin-friendly. For CPAP nasal pillows, this ensures a secure yet gentle seal around the nostrils without causing skin irritation, even with prolonged use.
Biocompatibility
LSR used in CPAP masks is medical-grade, meaning it meets rigorous biocompatibility and toxicity standards. It does not leach chemicals and is safe for contact with human skin and mucous membranes.
Durability and Hygiene
CPAP masks with liquid silicone pillows are resistant to high temperatures, UV light, and cleaning agents, making them suitable for repeated sterilization and long-term use.
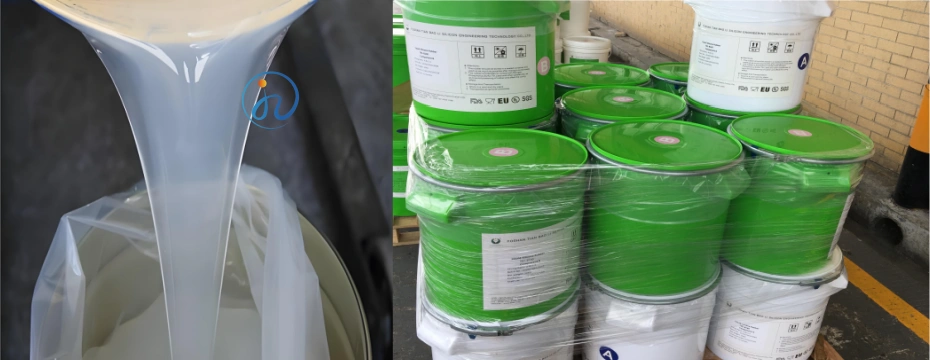
2. Key Components of a CPAP Mask with Silicone Pillow
A standard CPAP mask with a silicone pillow consists of:
- Nasal Pillow Cushion: The part that directly contacts the nose, made from liquid silicone rubber.
- Frame Assembly: Typically made of plastic or polycarbonate.
- Headgear Straps: Adjustable straps that secure the mask.
- Valve and Tube Connector: Interface with the CPAP machine.
Among these, the silicone pillow is the most sensitive and critical component, requiring precision manufacturing.
3. Step-by-Step Manufacturing Process of CPAP Masks Liquid Silicone Pillow
Step 1: Material Selection
Choose a medical-grade liquid silicone rubber (such as Dow Corning, Wacker, or Momentive) that meets ISO 10993 and USP Class VI standards. The LSR should have:
- Shore A hardness between 10–20 for flexibility
- High tear strength for durability
- Good elongation and rebound performance
Step 2: Mold Design and Prototyping
The mold must be designed with extreme precision to match the nasal anatomy and ensure a leak-proof seal. Key considerations include:
- 3D modeling of the nasal pillow shape
- Flow simulation to predict LSR behavior in the mold
- Venting channels for air evacuation
- Steel mold fabrication with mirror-polished cavity surfaces
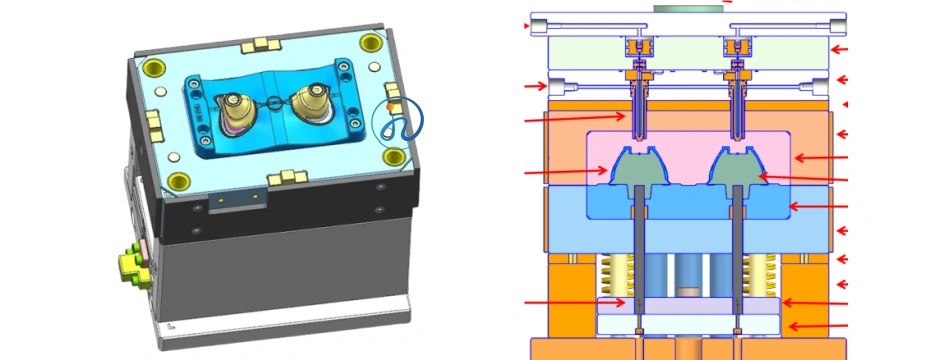
Step 3: LSR Injection Molding
LSR injection molding is the most reliable method for producing CPAP mask liquid silicone pillows.
Process Overview:
- Mixing: Two-part LSR is metered and mixed in a 1:1 ratio.
- Injection: The mixture is injected into a heated steel mold using a cold runner system.
- Curing: The mold temperature (150–180°C) triggers a rapid curing reaction within 30–60 seconds.
- Demolding: After curing, the part is automatically ejected.
Advantages:
- Flash-free molding
- Low cycle times
- High dimensional accuracy
- Consistent part quality
Step 4: Post-Curing (Optional)
Although LSR cures completely in the mold, a post-curing process in an oven (at 200°C for 2–4 hours) may be used to:
- Remove residual volatiles
- Enhance mechanical properties
- Ensure FDA compliance
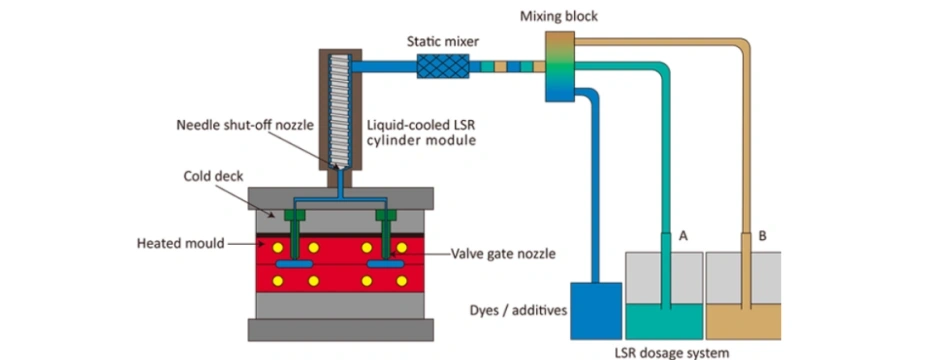
Step 5: Trimming and Surface Treatment
Any minor flash or parting lines are trimmed manually or using automated vision-guided systems. Optional surface treatments include:
- Plasma treatment to enhance bonding
- Texturizing for anti-slip properties
4. Assembly of the Complete CPAP Mask
After the silicone pillow component is molded:
- It is assembling into the plastic mask frame using snap-fit or adhesive bonding.
- Headgear straps and valves are adding.
- Each assembled mask undergoes air leak testing and fit verification.
5. Quality Control and Certification
Inspection Protocols:
- Visual Inspection: Check for air bubbles, discoloration, or flash.
- Dimensional Testing: Ensure accuracy using 3D scanners or gauges.
- Material Testing: Shore hardness, tensile strength, and tear resistance.
- Biocompatibility Testing: Cytotoxicity, sensitization, and irritation testing.
Certifications Required:
- ISO 13485 (Medical Device Manufacturing)
- CE or FDA 510(k) (for CPAP device approval)
- RoHS and REACH (for material safety compliance)
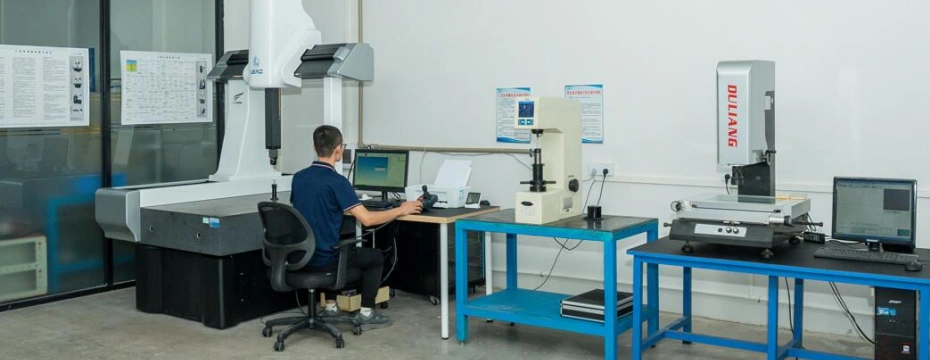
6. Packaging and Sterilization
Each CPAP mask is packing in medical-grade PE bags in a cleanroom environment. Some masks are delivering pre-sterilized using:
- Ethylene oxide (EO) sterilization
- Gamma radiation
- Steam sterilization (if material allows)
Proper labeling is essential to meet global regulatory guidelines.
7. Common Challenges in Manufacturing
- Material Flow Issues: Require optimized gating and venting.
- Shrinkage Variability: Can impact fit; requires mold compensation.
- Adhesion Problems: Addressed with surface activation or primer.
- Tooling Costs: High upfront mold investment, especially for multiple sizes.
8. Trends and Innovations
- 3D scanning of patient noses for custom-fit nasal pillows
- Smart CPAP masks with sensors embedded in the silicone
- Recyclable LSR materials for sustainable manufacturing
Conclusion
Producing CPAP masks with liquid silicone pillow components is a highly specialized process that requires advanced materials, precision tooling, and strict quality controls. By leveraging LSR injection molding, manufacturers can ensure consistent, safe, and comfortable nasal pillows that meet the needs of CPAP users worldwide.
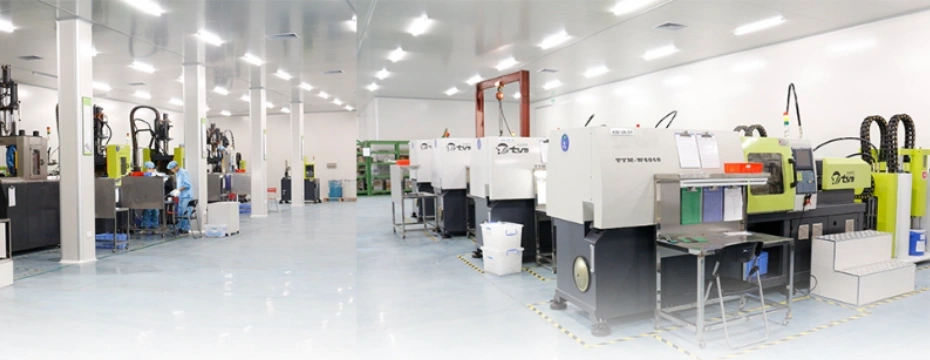
If you’re sourcing a reliable partner for custom CPAP silicone components, make sure to choose a manufacturer with medical-grade LSR expertise, ISO 13485 certification, and cleanroom production capabilities.