Table of Contents
ToggleSilicone injection molding machines are the cornerstone equipment for manufacturing high-quality silicone products, and their significance in modern manufacturing is self-evident. Not only do they ensure the precision and quality of silicone products, but through continuous technological advancements, they have greatly improved production efficiency and product quality. The evolution of silicone injection molding technology mirrors the development of the manufacturing industry, propelling the production of silicone products towards higher efficiency, greener practices, and smarter operations.
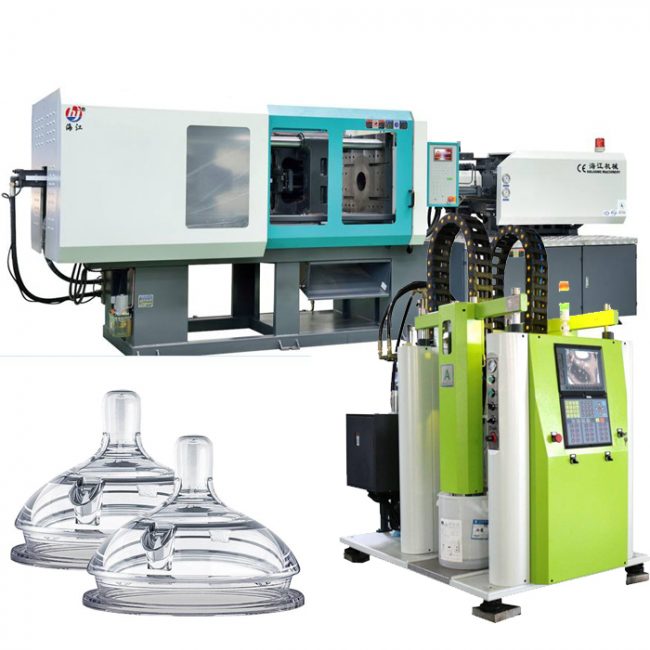
Technological Advancements in Silicone Injection Molding Machines
Automation and Control Systems
The automation and control systems of modern silicone injection molding machines are one of their core advantages. Through advanced software and hardware technologies, manufacturers can achieve precise control and monitoring, ensuring stability in the production process and consistency in product quality.
Rapid Cooling and Heating Systems
New cooling and heating systems have significantly enhanced the curing and processing speed of silicone, not only shortening the production cycle but also improving product quality and output to some extent.
Smart Manufacturing and Silicone Injection Molding Machines
Real-time Monitoring and Data Analysis
Through real-time monitoring and data analysis, manufacturers can instantly understand various parameters during the production process, promptly identify and resolve issues, thereby improving production efficiency and product quality.
Remote Diagnosis and Maintenance
Remote diagnosis and maintenance functionalities provide tremendous convenience for equipment maintenance, lowering maintenance costs and increasing equipment availability and production efficiency.
Environmental Protection and Sustainable Production
Energy Efficiency Optimization
Energy efficiency optimization is one of the crucial directions in the technological development of silicone injection molding machines. It helps to reduce energy consumption, lower production costs, and positively impacts environmental protection and sustainable production.
Waste Recycling and Reuse
Waste recycling and reuse not only reduce production costs but also help mitigate environmental impacts during production, paving the way for green manufacturing.
Application of Silicone Injection Molding Machine Technology by Jiaze Silicone
Driven by the technology of silicone injection molding machines, Jiaze Silicone continually explores innovation, especially in the maternal and infant health sectors. By applying the latest Liquid Silicone Rubber (LSR) Injection Molding technology, we offer a range of high-quality, safe, and efficient product solutions to our customers.
Case Study 1: Maternal and Infant Products
In the maternal and infant sector, safety and comfort are paramount. Jiaze Silicone utilizes advanced LSR injection molding technology to design and manufacture a range of silicone products for newborns and infants, such as anti-spill breast pads, soothing pacifiers, and silicone tableware. Our LSR injection molding technology ensures that the products are safe, non-toxic, soft, comfortable, and easy to clean, earning high praise from consumers. Moreover, the rapid production cycle and efficient manufacturing processes enable us to quickly respond to market demands and satisfy various customization needs.
Case Study 2: Medical Health Products
Medical health products often need to meet strict quality and safety standards. We employ LSR injection molding technology to produce a variety of medical silicone products, such as respiratory masks, medical catheters, menstrual cup, and various valves and seals. These products not only possess excellent biocompatibility, high-temperature resistance, and corrosion resistance, but also achieve precise dimensions and good sealing performance. At the same time, our efficient production flow and stringent quality control system ensure that every product meets medical device standards and customer expectations.
LSR injection molding technology
Jiaze Silicone has successful experience in applying LSR injection molding technology in maternal, infant, and medical health sectors. Our expertise and advanced technology enable us to provide customers with high-quality, efficient, and safe silicone product solutions, meeting the demands of various industries and applications.
Future Outlook
With the continuous advancement of Industry 4.0 and the maturation of artificial intelligence technology, future silicone injection molding machines will display trends towards more intelligent, efficient, and environmentally friendly development. These technological advancements will not only greatly improve the efficiency and quality of silicone product production but also bring about broader application possibilities and more business opportunities for the silicone product industry.
1. Intelligence:
Real-time Monitoring and Adaptive Control Systems: Next-generation silicone injection molding machines will be equipped with more advanced real-time monitoring systems and adaptive control technologies, capable of real-time monitoring of key parameters such as temperature, pressure, and cycle time during the production process. Through adaptive algorithms, real-time adjustments will ensure the stability of the production process and the controllability of product quality.
Predictive Maintenance: By analyzing a large amount of operational data, predictive maintenance technology can identify potential issues before equipment failure, thereby reducing maintenance costs and improving equipment availability and production efficiency.
2. Efficiency:
High-Speed Injection and Closed-Loop Control: The adoption of high-speed injection technology and closed-loop control systems will ensure precise control of injection speed and pressure, shorten the production cycle, and improve production efficiency.
Multifunctional Integration: Future silicone injection molding machines will integrate more functions, such as automatic feeding, online quality inspection, etc., to realize one-stop production, reduce production costs, and improve production efficiency.
3. Environmental Protection and Sustainable Production:
Energy Efficiency Optimization: By optimizing mechanical structures and control systems, energy efficiency will be improved, energy consumption will be reduced, and the silicone injection molding process will become more environmentally friendly.
Waste Recycling and Reuse Technology: Utilizing advanced waste recycling and reuse technologies to reduce waste during production will enable the sustainable development of silicone product production.
As these innovative technologies continue to be integrated into silicone injection molding machines, Jiaze Silicone will keep pace with industry development trends, continue to invest in research and development, enhance production efficiency and product quality, meet the demands of different industries and customers, and contribute to the development of the silicone product industry.
Conclusion
The continuous progression of silicone injection molding machine technology provides robust support for silicone product production. As a professional manufacturer of customized silicone products, Jiaze Silicone, leveraging advanced silicone injection molding machine technology, can offer customers superior and more efficient solutions. Additionally, through silicone injection molding technology, we can better meet the needs of various industries and customers.