Table of Contents
ToggleLiquid Silicone Rubber (LSR) is widely used in industries like healthcare, automotive, electronics, and baby care due to its superior performance. However, the full value of LSR can only be realized when strict quality solutions are in place. LSR quality solutions are not just about meeting standards—they are about minimizing defects, maximizing safety, and delivering consistent performance.
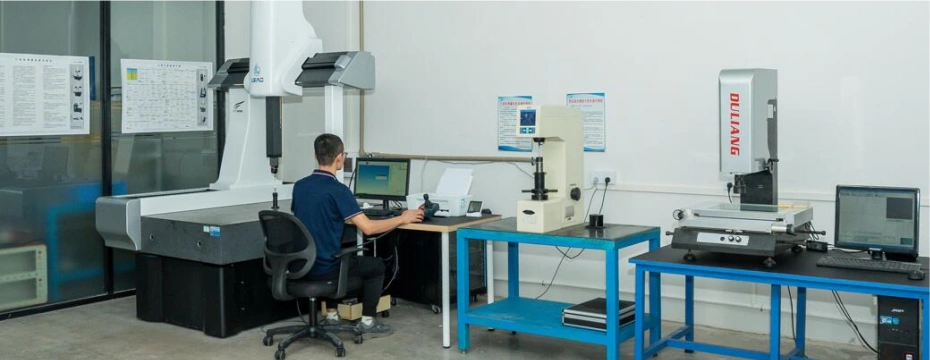
1. What Are LSR Quality Solutions?
LSR Quality Solutions refer to the systems, tools, and processes used to monitor, control, and improve the quality of liquid silicone rubber products throughout their production lifecycle.
They include:
- Raw material verification
- Mold validation and process monitoring
- In-process inspection
- Final product testing
- Documentation and traceability
These steps help prevent contamination, ensure biocompatibility, and maintain dimensional stability—especially critical for medical-grade and food-contact LSR components.
2. Key Elements of a Robust LSR Quality System
2.1 Incoming Material Inspection
- Platinum-cured silicone base and catalyst are checked for purity.
- Material traceability ensures every batch meets specifications.
2.2 Process Control During LSR Injection Molding
- Real-time monitoring of temperature, pressure, and injection speed.
- Use of closed-loop systems to prevent defects like short shots, air entrapment, or flash.
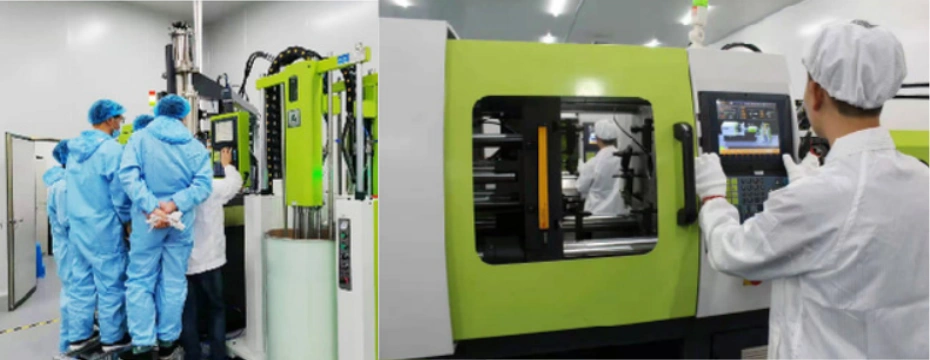
2.3 In-Process Inspection
- Cavity pressure sensors and optical systems detect anomalies during molding.
- Automatic rejection systems remove non-conforming parts immediately.
2.4 Post-Molding Quality Checks
- Dimensional analysis with 2D/3D measuring equipment.
- Tensile strength, elongation, and hardness tests to ensure mechanical integrity.
- Visual inspection for clarity, surface finish, and flash.
3. LSR Quality Standards and Certifications
Compliance with international standards ensures product reliability and market acceptance:
- ISO 9001: General quality management system
- ISO 13485: Medical device quality management
- FDA 21 CFR 177.2600: Food-contact LSR compliance
- USP Class VI: Biocompatibility certification for medical LSR
Manufacturers adhering to these standards demonstrate a commitment to quality and risk mitigation.
4. Advanced Testing Technologies in LSR Production
Modern LSR manufacturers invest in advanced testing tools for faster and more accurate QA:
- FTIR Analysis: Ensures chemical consistency
- X-Ray and CT Scanning: Non-destructive analysis of complex geometries
- Automated Vision Systems: High-speed defect detection at micron levels
- Cleanroom Production: For critical applications like catheters, valves, and respirators
These tools are vital for industries like healthcare and automotive, where zero-defect tolerance is often the rule.
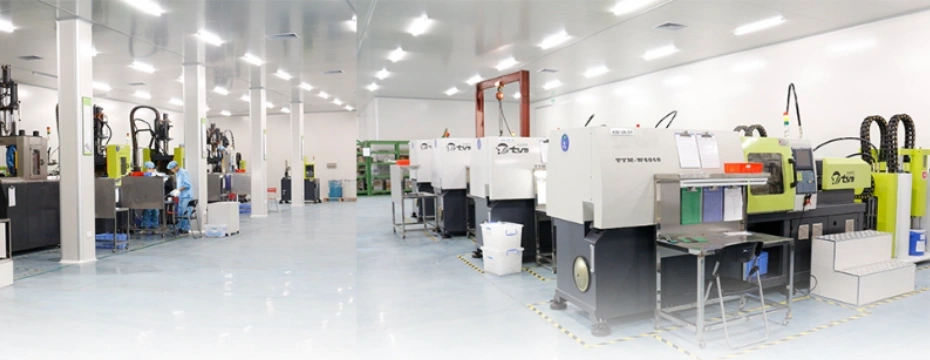
5. LSR Defect Prevention: From Design to Delivery
Quality solutions should start before production:
- DFM (Design for Manufacturability): Reduce complexity and tolerance issues.
- Tooling Validation: Proper mold design avoids burrs, short shots, or deformations.
- Process Validation (IQ, OQ, PQ): Especially critical for regulated sectors like medtech.
Once production begins, statistical process control (SPC) and Six Sigma techniques help reduce variability and enhance repeatability.
6. Benefits of Implementing LSR Quality Solutions
Higher Customer Satisfaction
Fewer Returns or Recalls
Cost Savings Through Waste Reduction
Faster Time to Market
Stronger Regulatory Compliance
Whether you’re producing infant care products, medical seals, or automotive gaskets, LSR quality solutions protect both your brand and your end users.
7. Choosing the Right LSR Manufacturer with Quality Expertise
When selecting an LSR supplier, consider the following:
- Do they have ISO 13485 or FDA registration?
- Do they provide traceability reports and PPAP?
- Can they support cleanroom production and post-curing processes?
A manufacturer that offers end-to-end quality control will ensure your custom LSR components meet the highest performance expectations.
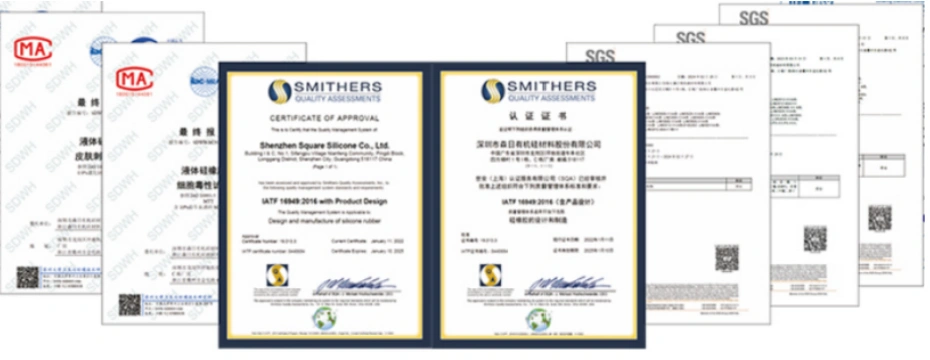
Conclusion: Quality Is Not Optional in LSR Manufacturing
In high-performance applications, even a microscopic defect in LSR components can lead to product failure, safety risks, or compliance issues. That’s why investing in comprehensive LSR Quality Solutions—from raw material validation to final inspection—is critical.
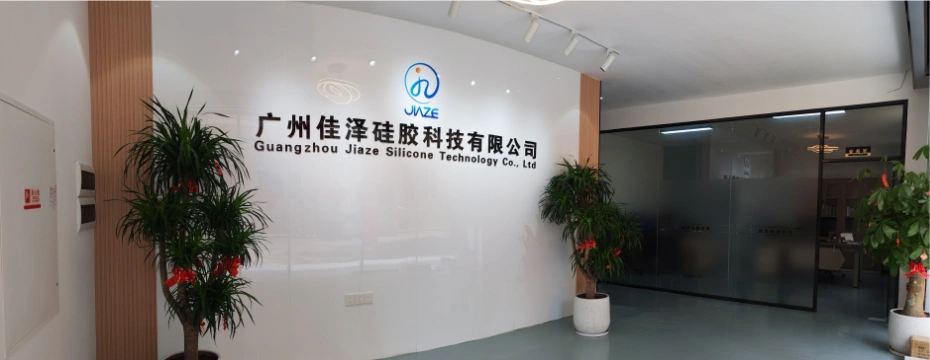
Work with a trusted LSR partner that integrates precision engineering, robust quality systems, and industry certifications into every stage of production.