Table of Contents
ToggleIn the world of modern product design, selecting the right materials and manufacturing processes is critical for achieving durability, functionality, and user satisfaction. One process that continues to gain popularity is LSR overmolding. But when exactly is it the best solution?
This article explains when LSR overmolded components offer the greatest advantages, helping product developers and manufacturers make informed decisions.
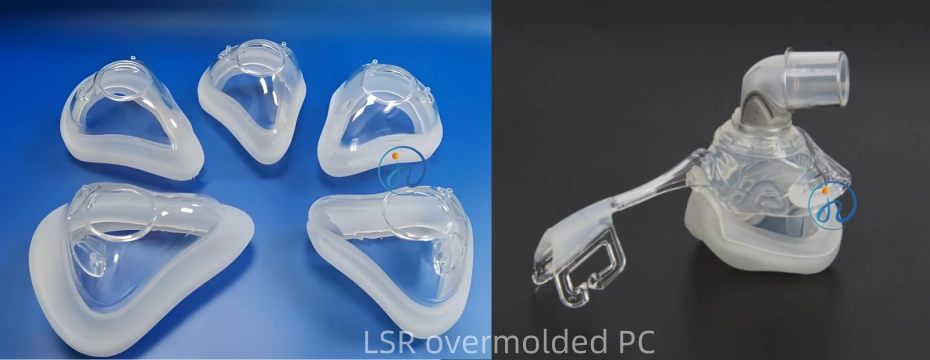
What Does LSR Overmolded Mean?
LSR overmolded refers to components created by overmolding Liquid Silicone Rubber (LSR) onto another substrate material, such as plastic, metal, or other rigid components. The result is a seamless, integrated product that combines the strength of the base material with the softness, flexibility, and durability of silicone.
When Is LSR Overmolded the Best Choice?
The LSR overmolded process is ideal for products that require:
1. Superior Sealing and Waterproofing
Products exposed to moisture, dust, or harsh environmental conditions greatly benefit from LSR overmolding. The silicone forms a watertight and dustproof barrier, making it perfect for:
- Medical devices
- Wearable electronics
- Automotive connectors
- Outdoor equipment
2. Enhanced Grip and Ergonomics
When user comfort and anti-slip features are essential, LSR overmolded surfaces provide a soft-touch feel and improved handling. Common examples include:
- Baby products (bottle grips, pacifiers)
- Handheld medical devices
- Tool handles
- Sports equipment
3. Vibration and Shock Absorption
For products exposed to impact, vibration, or repeated stress, LSR overmolding adds a protective layer that absorbs shocks and reduces wear, such as:
- Automotive parts
- Industrial equipment components
- Electronic housings
4. Biocompatibility for Medical and Personal Care
LSR materials used in overmolding are often medical-grade and biocompatible, making them ideal for products that come into direct contact with the skin or body, such as:
- Respiratory masks
- CPAP nasal pillows
- Medical seals and gaskets
- Personal care products
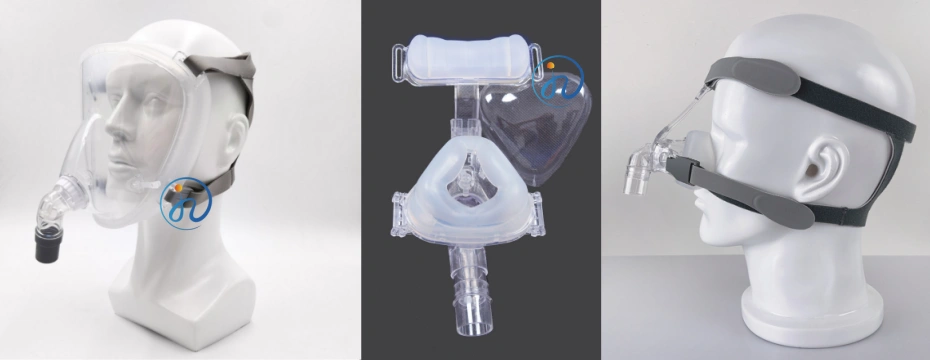
5. Chemical and Temperature Resistance
In demanding environments where exposure to chemicals, oils, or extreme temperatures is a concern, LSR overmolded components maintain their integrity, making them suitable for:
- Automotive engine parts
- Industrial seals
- Food-grade applications
Key Industries That Benefit from LSR Overmolded Components
Medical Industry
- Catheter components
- Wearable health monitors
- Seals and valves for medical devices
Automotive Industry
- Electrical connectors
- Engine gaskets
- Sensor housings
Consumer Electronics
- Waterproof headphones
- Smartphone grips
- Smartwatch seals
Personal Care and Baby Products
- Pacifiers
- Baby bottle components
- Oral care devices
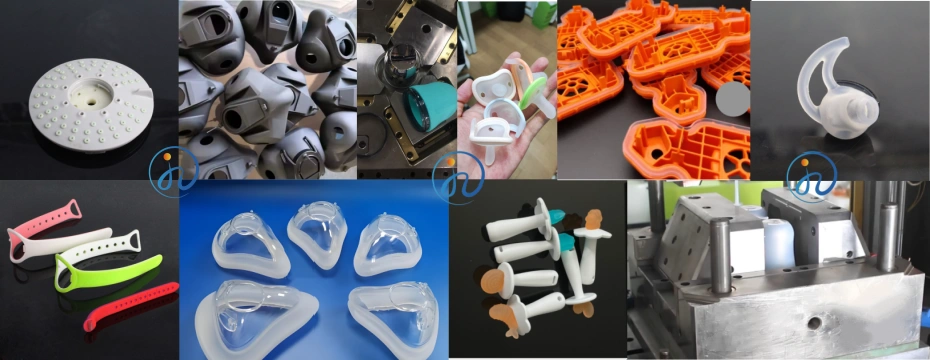
Advantages of Choosing LSR Overmolded Products
Strong bonding between materials
Enhanced product durability
Reduced part count and assembly steps
Improved product aesthetics and functionality
Compliance with medical and food safety standards
When Should You Avoid LSR Overmolding?
While LSR overmolded components offer many benefits, there are situations where this process may not be ideal, such as:
- Very low production volumes (due to tooling costs)
- Products not exposed to environmental or mechanical stress
- When bonding between materials is incompatible
In such cases, simpler assembly methods or alternative materials may be more cost-effective.
Conclusion
LSR overmolded components are the best choice when products demand enhanced durability, sealing, comfort, and biocompatibility. This process enables manufacturers to create high-performance parts that meet the strict requirements of medical, automotive, and consumer industries.
If you’re designing a product that needs superior sealing, flexibility, and durability, LSR overmolding is worth considering.

Working with an experienced manufacturer that has the experience and knowledge of the tooling and LSR overmolding process, and an understanding of the nuances and differences between LSRs and thermoplastics is mandatory. It can make the difference between success and failure.