Table of Contents
ToggleIn today’s kitchenware industry, material safety and performance are top priorities for both manufacturers and consumers. Among various material choices, Liquid Silicone Rubber (LSR) has emerged as a premium solution for kitchen products due to its exceptional thermal resistance, biocompatibility, design flexibility, and long service life. Whether you’re producing spatulas, bakeware, food molds, or sealing components, LSR is increasingly becoming the material of choice.
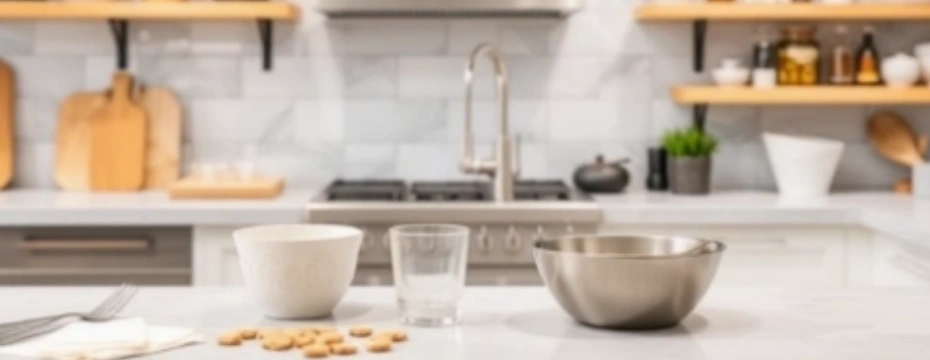
In this article, we’ll explore the many advantages of using LSR for kitchen products, how it compares to traditional materials, and why manufacturers and designers are turning to LSR for high-performance, consumer-safe kitchen applications.
1. What Is LSR (Liquid Silicone Rubber)?
Liquid Silicone Rubber (LSR) is a two-part platinum-cured silicone that is injected into molds using specialized injection molding equipment. It’s known for its high purity, flexibility, resistance to extreme temperatures, and excellent performance in food contact applications.
Unlike solid silicone or thermoplastics, LSR remains flexible across a wide range of temperatures and offers superior chemical stability and resistance to deformation.
2. Advantages of LSR in Kitchen Products
2.1 Food Safety and Compliance
LSR is FDA-compliant, BPA-free, and approved for direct food contact. It meets regulations such as:
- FDA 21 CFR 177.2600
- LFGB (German Food Code)
- REACH and RoHS standards
This makes LSR ideal for food-grade kitchen products like baby spoons, baking mats, cake molds, and storage lids.
2.2 Heat and Cold Resistance
LSR can withstand extreme temperatures ranging from -60°C to +250°C (-76°F to +482°F) without degrading. This property is essential for kitchen products used in:
- Ovens and microwaves
- Freezers
- Dishwashers
It doesn’t warp, melt, or release toxic fumes when exposed to heat.
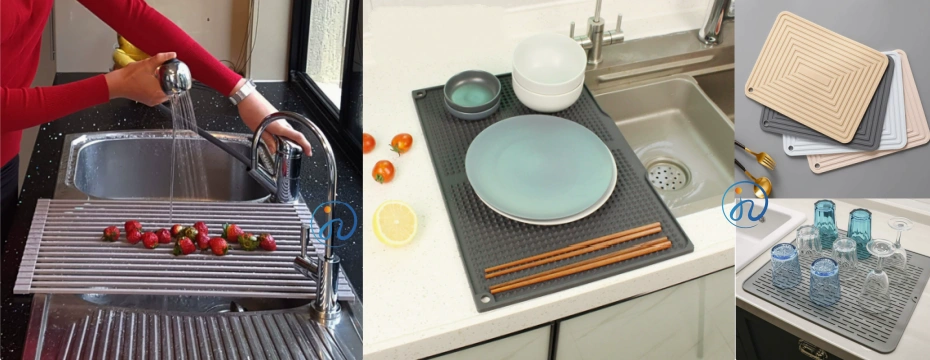
2.3 Flexibility and Elasticity
Whether you’re designing a collapsible bowl or a stretchable lid, LSR offers outstanding elastic recovery and soft-touch flexibility, making it perfect for ergonomic handles, grips, and seals.
2.4 Non-Stick and Easy to Clean
Thanks to its non-stick surface, food residue does not cling to LSR kitchen items. It’s also dishwasher-safe, stain-resistant, and easy to sterilize. This improves hygiene and reduces cleaning time.
2.5 Durability and Longevity
LSR products resist:
- Tearing and abrasion
- UV and ozone exposure
- Frequent mechanical stress
Compared to plastics or rubber, LSR products last longer and maintain their shape and color after repeated use and washing.
3. Common Kitchen Products Made with LSR
Manufacturers use LSR to produce a variety of innovative and safe kitchen items, including:
- Silicone baking mats and trays
- Cooking spatulas and scrapers
- Sealing rings and gaskets for pressure cookers
- Ice cube and chocolate molds
- Collapsible bowls and measuring cups
- Lids and stretchable food covers
- Baby food containers and pacifiers
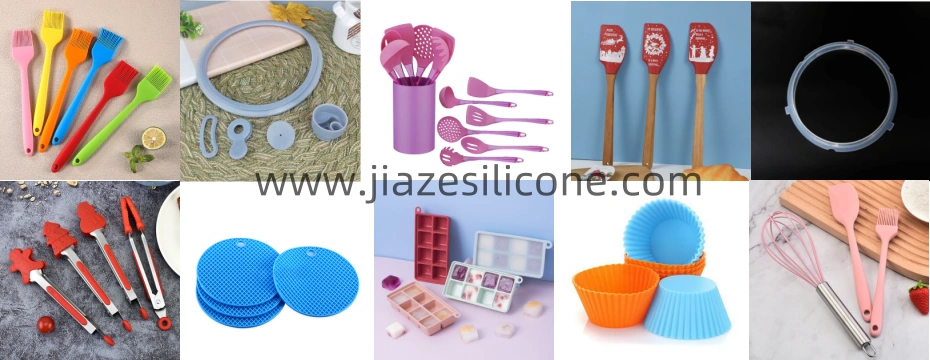
4. LSR vs. Traditional Kitchenware Materials
Feature | LSR | Thermoplastics (PP/PE) | Metal or Steel |
---|---|---|---|
Food Safety | FDA and LFGB compliant | May contain BPA or phthalates | Requires coating or treatment |
Temperature Resistance | -60°C to 250°C | 0°C to 100°C | Up to 300°C, but can overheat |
Flexibility | Excellent | Low to moderate | None |
Non-Stick Surface | Yes | No | No |
Dishwasher Safe | Yes | Sometimes | Usually, but may rust |
Product Lifespan | Long | Medium | Long, but heavier and rigid |
5. Why Manufacturers Prefer LSR for Kitchen Products
5.1 Precision Injection Molding
LSR supports automated injection molding, allowing for:
- High-volume production
- Tight tolerances and repeatability
- Complex geometries and micro-features
- Minimal material waste
This is essential for manufacturers aiming to scale production while maintaining product quality.
5.2 Design Flexibility
LSR molds can include intricate textures, branding elements, and custom shapes. It enables product designers to innovate without sacrificing function or aesthetics.
5.3 Seamless Overmolding Capability
LSR can be overmolded onto:
- Plastics (e.g., nylon, PPSU)
- Metals
- Glass
This is particularly useful for making multi-material kitchen tools like ergonomic silicone handles bonded to stainless steel blades.
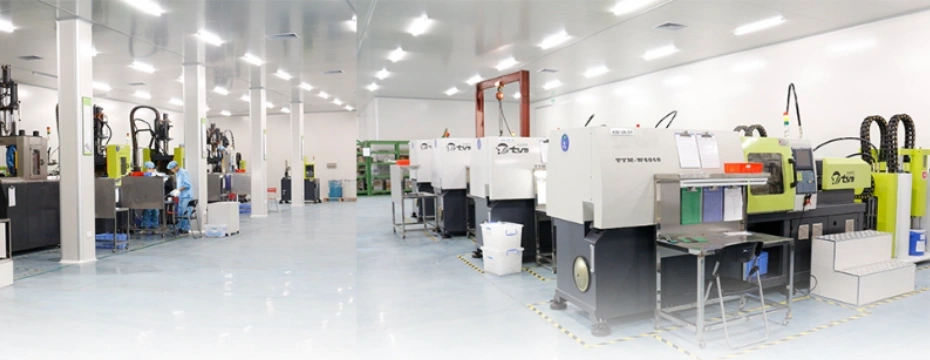
6. Sustainability and Eco-Friendliness
As environmental concerns grow, LSR is gaining attention as a more sustainable option:
- Long product lifespan means fewer replacements and less waste.
- LSR can be recycled in industrial processes.
- It’s inert and doesn’t leach chemicals into food or the environment.
- No VOCs are released during production or use.
7. Market Trends in LSR Kitchenware
With increasing consumer demand for:
- Non-toxic materials
- Colorful and stylish kitchen tools
- Multi-functional products
LSR is poised to continue its growth in the kitchen products segment. Brands like OXO, Lekue, and Joseph Joseph are already leveraging LSR for high-end kitchenware.
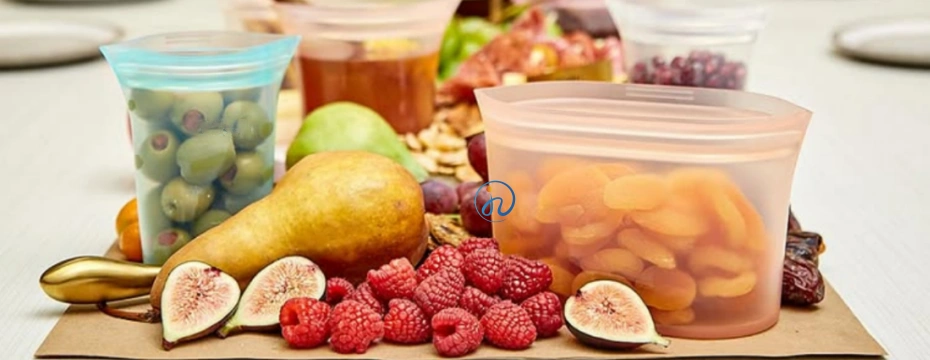
8. Challenges and Considerations
While LSR offers numerous benefits, manufacturers should also consider:
- Higher tooling costs for LSR injection molds
- Specialized equipment and processing knowledge
- Material cost, which is higher than basic plastics
However, the long-term ROI often outweighs the initial investment due to reduced defects, longer product life, and improved customer satisfaction.
Conclusion: Is LSR the Future of Kitchen Products?
Absolutely. For brands seeking to combine safety, performance, and aesthetic design, Liquid Silicone Rubber stands out as a premium material choice. From bakeware to utensils and food storage solutions, LSR meets the modern consumer’s expectations for healthy, high-quality, and long-lasting kitchen products.
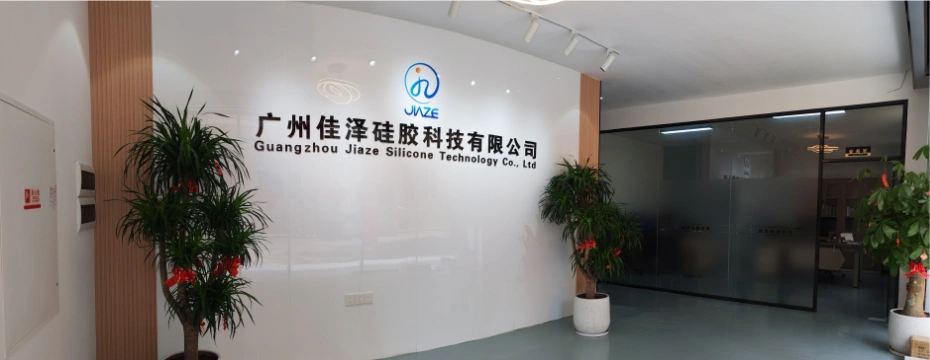
As the demand for eco-friendly and user-friendly materials rises, manufacturers who adopt LSR for kitchen products will not only meet industry standards but also build stronger brand trust and product differentiation.