Table of Contents
ToggleLSR’s ability to maintain its mechanical properties in extreme temperatures (with thermal stability from -50 degrees C to 250 degrees C) make it ideal for exterior automotive components. Rubber components in the engine compartment, seals and diffusers in headlights, as well as vibration dampeners in climate control systems are continuously exposed to a vast range of heat and cold temperatures, and water and moisture. Liquid silicone rubber also offers superior elongation, and ozone and UV resistance for gaskets and other components exposed to the environment.
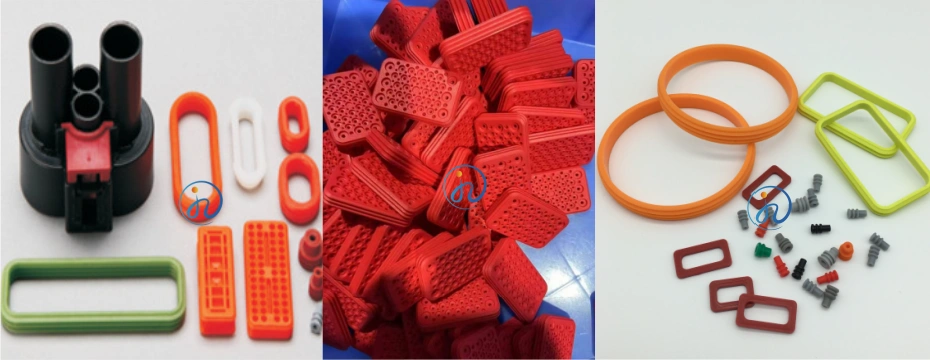
The automotive industry demands materials that can withstand extreme conditions: scorching engine heat, freezing temperatures, harsh chemicals, constant vibration, and the relentless pursuit of longevity and safety. While traditional elastomers have served their purpose, Liquid Silicone Rubber (LSR) has emerged as the superior engineered material for an ever-growing range of critical automotive components. But why is LSR increasingly the material of choice for engineers and designers? Let’s delve into the key benefits driving its adoption.
1. Unmatched Temperature Performance: From Deep Freeze to Blazing Heat
The Challenge: Automotive parts face wild temperature swings. Under-hood components bake near engines, while exterior parts endure freezing climates. Traditional rubbers crack, harden, or degrade.
The LSR Advantage: LSR excels where others fail. It maintains exceptional flexibility and performance across an incredibly wide range, typically -60°C to +200°C (-76°F to +392°F), with some grades exceeding +230°C (+446°F). This ensures:
- Reliable sealing of engine gaskets and coolant systems under high heat.
- Consistent performance of ignition components and sensor seals.
- Durability of exterior seals and grommets in harsh winter conditions.
2. Superior Sealing & Environmental Protection: Keeping Contaminants Out
The Challenge: Preventing ingress of moisture, dust, dirt, and fluids is critical for electrical systems, lighting, ECUs, and powertrain longevity. Seals must remain effective over years of compression set and environmental exposure.
The LSR Advantage: LSR offers outstanding compression set resistance, meaning it bounces back effectively after being squeezed, maintaining a tight seal long-term. Its inherent hydrophobicity (water-repelling nature) and excellent resistance to weathering, ozone, and UV light make it ideal for:
- Headlight and taillight seals.
- Electrical connector seals and grommets.
- Sensor housings and protective boots.
- Transmission and fuel system seals.
3. Exceptional Chemical Resistance: Standing Up to Automotive Fluids
The Challenge: Automotive parts are constantly exposed to aggressive fluids: engine oils, transmission fluids, brake fluids, coolants, and fuels. Degradation can lead to leaks, swelling, and failure.
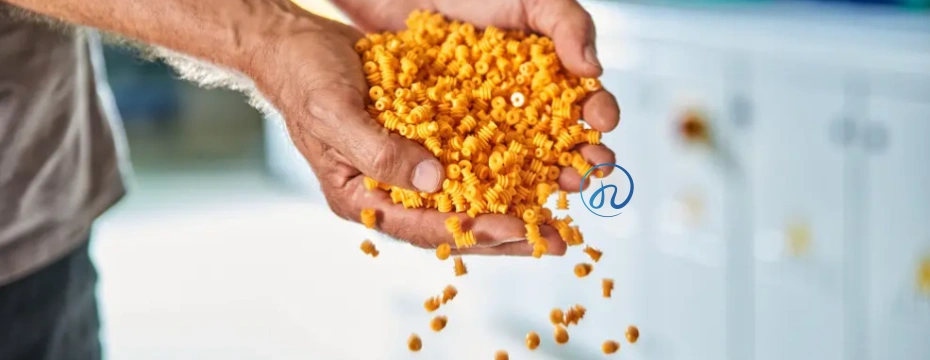
The LSR Advantage: LSR demonstrates excellent resistance to a wide range of automotive fluids and chemicals. It generally resists swelling, hardening, or losing its physical properties when exposed to oils, greases, alcohols, coolants, and diluted acids/bases far better than many organic rubbers. This ensures:
- Long-lasting performance of seals in fuel systems, oil pans, and transmission housings.
- Integrity of fluid handling components.
- Reliability in applications exposed to cleaning agents.
4. Outstanding Durability & Long Service Life: Built to Last
The Challenge: Automotive components must last the lifetime of the vehicle, enduring constant stress, vibration, and environmental assault without failure.
The LSR Advantage: Combining its temperature stability, chemical resistance, and inherent flexibility, LSR parts offer exceptional long-term durability. They resist fatigue, cracking, and degradation, contributing directly to:
- Reduced warranty claims and maintenance costs.
- Enhanced vehicle reliability and safety.
- Meeting stringent OEM lifespan requirements.
5. Precision & Design Freedom: Enabling Innovation
The Challenge: Modern automotive design demands complex, miniaturized, and highly precise components. Manufacturing processes need to be efficient and consistent.
The LSR Advantage: LSR is processed using high-precision liquid injection molding (LIM). This offers significant benefits:
- Extreme Precision: Produces parts with tight tolerances, intricate geometries, and fine details (thin walls down to 0.2mm, microfluidic channels) impossible with many other elastomers.
- Efficiency & Consistency: Fast cycle times, excellent part-to-part consistency, and minimal post-processing (no deflashing needed for many parts).
- Overmolding/Bonding: LSR readily bonds to many thermoplastics (PP, PA, PBT, PC) and metals, enabling complex multi-material components like integrated seals, damped connectors, and tactile buttons.
- Design Innovation: Enables smaller, lighter, and more functional integrated parts.
6. Safety & Compliance: Meeting Stringent Standards
The Challenge: Automotive parts must comply with rigorous safety, emissions, and performance regulations (e.g., USP Class VI, FDA, ISO 10993, various OEM specifications, low VOC emissions).
The LSR Advantage: Medical-grade and automotive-grade LSR formulations are readily available. Key advantages include:
- High Purity: Low extractables and leachables.
- Biocompatibility: Suitable for fluid contact applications.
- Flame Retardancy: Meets UL 94 V-0 and automotive flame resistance standards, crucial for battery components and wiring.
- Low VOC/FOG: Minimizes outgassing that can cause fogging on windows or contaminate sensitive sensors.
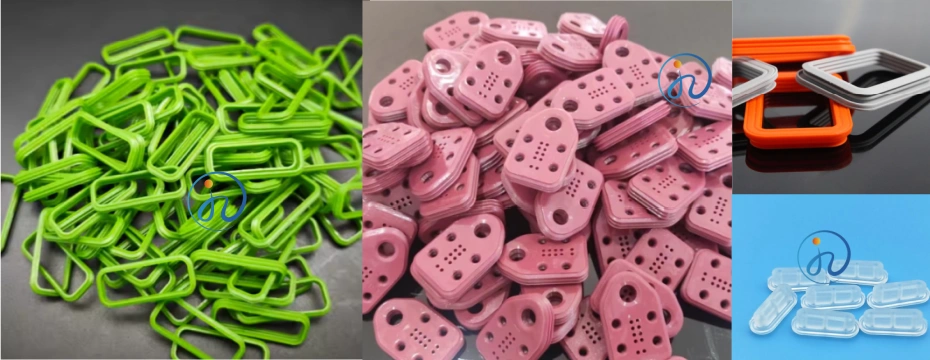
7. Critical for Electric Vehicle (EV) Advancement
The Challenge: EVs introduce new demands: high-voltage insulation, extreme battery pack temperatures, coolant management for batteries/motors, and stringent safety requirements.
The LSR Advantage: LSR is uniquely suited for the EV revolution:
- High Voltage Insulation: Excellent dielectric properties protect battery packs, connectors, and charging components.
- Battery Thermal Management: Seals for cooling plates and coolant hoses withstand both high temperatures and aggressive coolants.
- Flame Retardancy: Essential for battery pack safety components.
- Sealing Integrity: Protects sensitive electronics from moisture and contaminants in motors and battery enclosures.
Conclusion: LSR – The Smart Choice for Demanding Automotive Applications
Choosing the right material is fundamental to automotive part performance, safety, and longevity. Liquid Silicone Rubber (LSR) delivers a compelling combination of properties that directly address the harshest automotive environments and evolving technological demands. From its unparalleled temperature range and sealing capabilities to its chemical resistance, durability, precision manufacturability, and critical role in EVs, LSR provides engineers with a reliable, high-performance solution.