Table of Contents
ToggleAs the demand for sleek, durable, and high-performing consumer electronics parts continues to grow, manufacturers are constantly seeking materials that can withstand high temperatures, maintain flexibility, and deliver long-term reliability. Liquid Silicone Rubber (LSR) has emerged as a leading solution in this sector due to its unmatched versatility, biocompatibility, and precision molding capabilities.
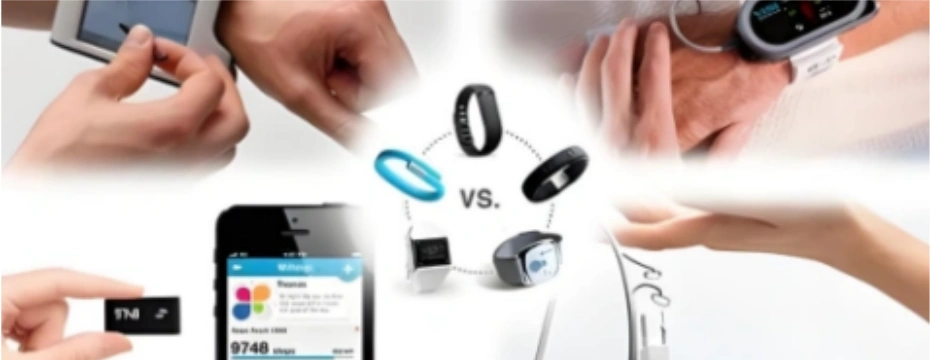
In this comprehensive guide, we’ll explore why LSR is the preferred material for consumer electronics components, how it compares to alternatives, its typical applications, and key benefits that drive innovation in the electronics industry.
1. Introduction to LSR and Its Relevance in Electronics
Liquid Silicone Rubber (LSR) is a thermosetting polymer known for its exceptional thermal stability, elasticity, and resistance to environmental factors. It is commonly processed using injection molding, which allows for complex part geometries and consistent quality—ideal for the tight tolerances required in electronics manufacturing.
Key Attributes of LSR:
- High heat resistance (up to 200–250°C)
- UV and ozone resistance
- Electrical insulation properties
- Non-toxic and biocompatible
- Soft-touch surface and excellent elasticity
These qualities make LSR an ideal material for a wide range of consumer electronics parts, including wearable devices, cable insulation, connectors, gaskets, and keypad components.
2. Why LSR Is the Optimal Choice for Consumer Electronics Parts
✅ A. Excellent Thermal Stability
Consumer electronics often generate heat during operation. LSR can withstand high temperatures without losing its mechanical integrity, ensuring device safety and longevity.
✅ B. Superior Electrical Insulation
LSR exhibits high dielectric strength and low conductivity, making it an excellent insulator for cables, housings, and other electronic components. This helps protect sensitive circuits from interference and failure.
✅ C. Precision Molding for Complex Designs
The injection molding process allows for high-precision, automated production of intricate parts. This is particularly valuable in electronics, where components must fit seamlessly into compact devices.
✅ D. Chemical and Environmental Resistance
LSR is resistant to chemicals, UV radiation, and ozone, ensuring that electronics parts made with LSR can endure harsh conditions without degrading—especially in outdoor or wearable applications.
✅ E. Lightweight and Flexible
With its inherent softness and low weight, LSR enables ergonomic designs in wearables and handheld devices without compromising strength or functionality.
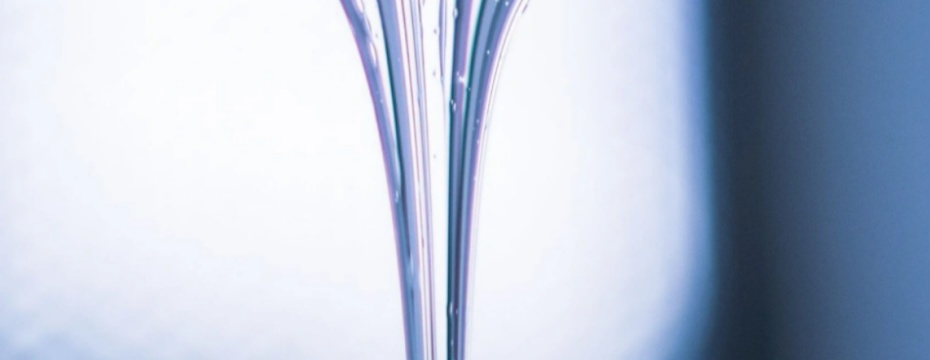
3. Common LSR Applications in Consumer Electronics
LSR is increasingly used across a broad spectrum of electronics, from personal gadgets to industrial-grade equipment. Here are some notable examples:
Smartphone and Tablet Components
- Button mats and keypads
- Gaskets and seals for waterproofing
- Wireless charging pads (soft-touch overmolding)
Wearable Technology
- Watch straps (e.g., Apple Watch bands)
- Fitness tracker housings
- Earbud tips and wearable gaskets
Cables and Connectors
- USB cable overmolding
- High-voltage insulators
- Charging port seals
Audio Devices
- Headphone cushions and seals
- Microphone diaphragms
- Speaker surrounds
Household Electronics
- Kitchen appliance seals and touchpads
- Smart thermostat covers
- Child-safe remote control buttons
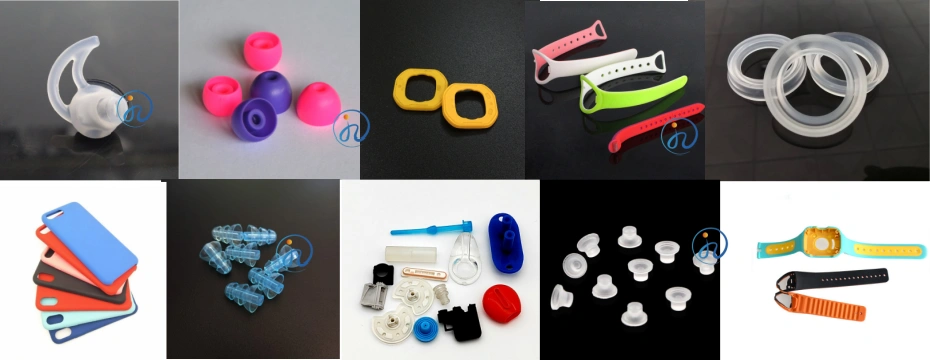
4. LSR vs. Traditional Materials for Electronics Parts
Property | LSR | Thermoplastics (e.g., TPE, TPU) | Conventional Silicone |
---|---|---|---|
Heat Resistance | Excellent | Moderate | Good |
Mold Precision | High | Medium | Medium |
Electrical Insulation | High | Moderate | High |
Durability | High | Varies | High |
Flexibility | Excellent | Good | Good |
Biocompatibility | Excellent | Moderate | Excellent |
While thermoplastics are often used for cost-sensitive parts, LSR provides superior durability, temperature performance, and design freedom, especially in premium consumer electronics parts.
5. Advantages for Manufacturers
🛠Efficient Production with LSR Injection Molding
LSR’s fast-curing nature and compatibility with automated injection molding make it ideal for mass production. Manufacturers can reduce cycle times and achieve consistent, high-quality parts.
💡 Reduced Assembly Needs
Due to its ability to form complex, integrated geometries, LSR reduces the need for multi-part assemblies, which simplifies production and lowers costs.
🔋 Improved Product Lifespan
LSR components are less likely to degrade or fail due to environmental exposure, contributing to longer-lasting devices and greater customer satisfaction.
6. Eco-Friendliness and Safety
As sustainability becomes a growing concern in electronics, LSR offers environmental advantages:
- Non-toxic and safe for skin contact (important for wearables)
- Long life cycle, reducing electronic waste
- Can be manufactured in cleanroom environments, essential for medical-grade or hygiene-focused electronics
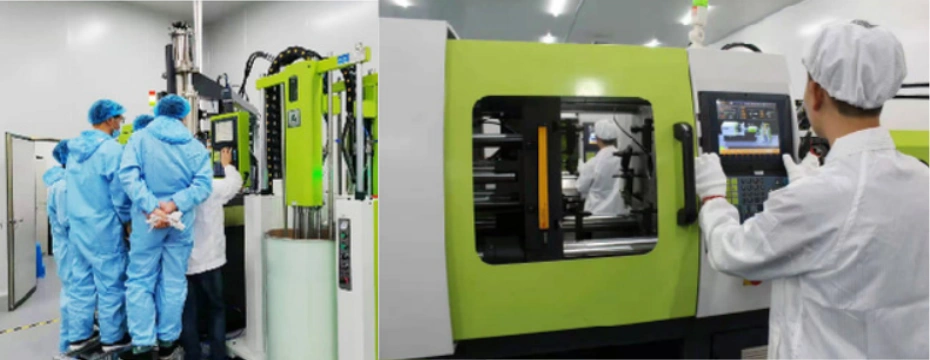
7. Real-World Examples: LSR in Action
📱 Apple Watch Bands
Made of medical-grade LSR, these bands are soft, durable, and skin-safe—ideal for all-day wear.
🎧 Noise-Canceling Earbuds
Many top-tier brands use LSR for ear tips due to its ability to conform to the ear canal and enhance acoustic performance.
🖥 Waterproof Smartphones
LSR seals and gaskets help ensure IP68 water resistance standards are met, protecting internal components from water and dust.
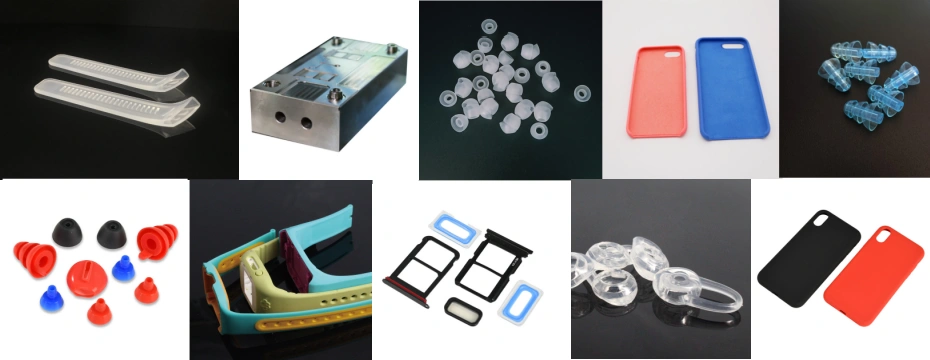
8. Challenges and Considerations
While LSR offers many advantages, there are some considerations:
- Tooling cost: Initial mold design and tooling can be expensive.
- Material cost: LSR is often more costly than thermoplastics.
- Processing expertise: Requires specialized knowledge in LSR molding to optimize material properties.
However, the long-term ROI in product quality, brand reputation, and customer satisfaction often outweighs the initial investment.
9. Conclusion
Liquid Silicone Rubber (LSR) is increasingly being adopted in the consumer electronics industry due to its reliability, flexibility, and outstanding performance characteristics. Whether it’s for wearable devices, smartphones, or high-end audio equipment, LSR offers unmatched advantages that help brands deliver durable, user-friendly, and high-performance products.
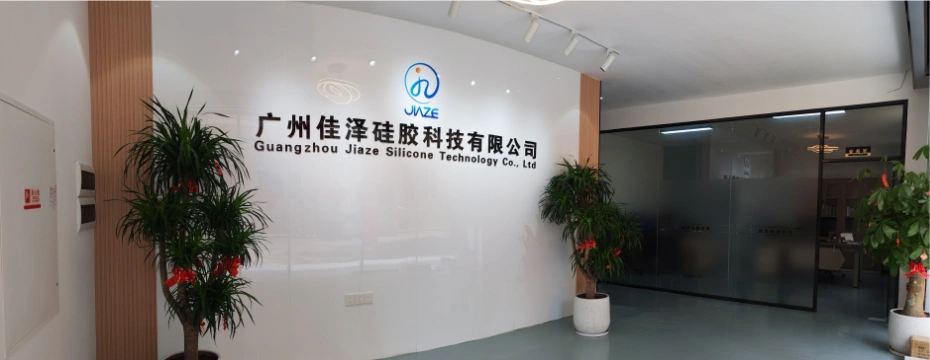
For manufacturers and engineers looking to stay ahead in a competitive electronics market, choosing LSR for consumer electronics parts isn’t just a smart move—it’s a strategic advantage.