Table of Contents
ToggleIn the fast-evolving medical industry, the materials used to manufacture products play a vital role in ensuring patient safety, product durability, and manufacturing efficiency. One material that has gained significant popularity is Liquid Silicone Rubber (LSR). Known for its biocompatibility, flexibility, and excellent mechanical properties, LSR medical products are transforming the way healthcare devices are designed and produced.
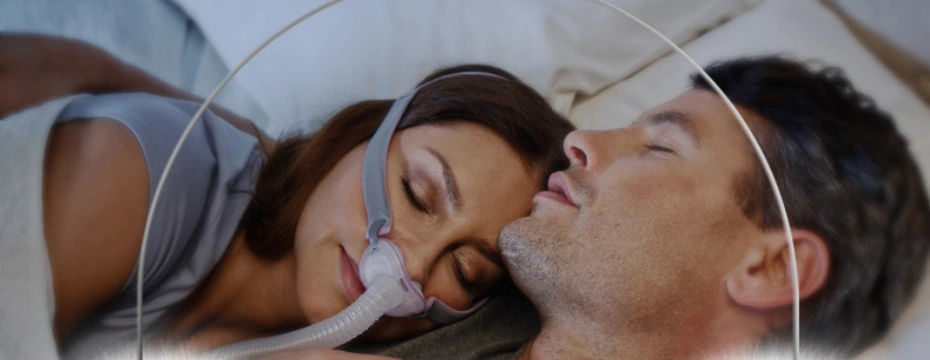
This article explores why Liquid Silicone Rubber is the material of choice for many medical device manufacturers and how it meets the strict standards of modern healthcare.
1. What is LSR? A Brief Overview
Liquid Silicone Rubber (LSR) is a two-part platinum-cured silicone material that is processed through liquid injection molding. It differs from traditional high-consistency rubber (HCR) by its low viscosity and ability to fill molds with complex geometries. This makes LSR ideal for mass production of detailed medical components.
Key Characteristics of LSR:
- Low viscosity for efficient injection molding
- High thermal stability and flexibility
- Transparent or can be pigmented
- Chemically inert and hypoallergenic
2. Why LSR is Ideal for Medical Applications
2.1. Biocompatibility and Hypoallergenic Properties
One of the most critical requirements in medical applications is biocompatibility. LSR has been rigorously tested and certified to meet ISO 10993 and USP Class VI standards, making it safe for direct contact with human tissue and fluids. It’s also hypoallergenic and free from latex, minimizing the risk of allergic reactions.
Examples:
- Catheters
- Respirator masks
- Nasal pillows
- Sealing gaskets for infusion sets
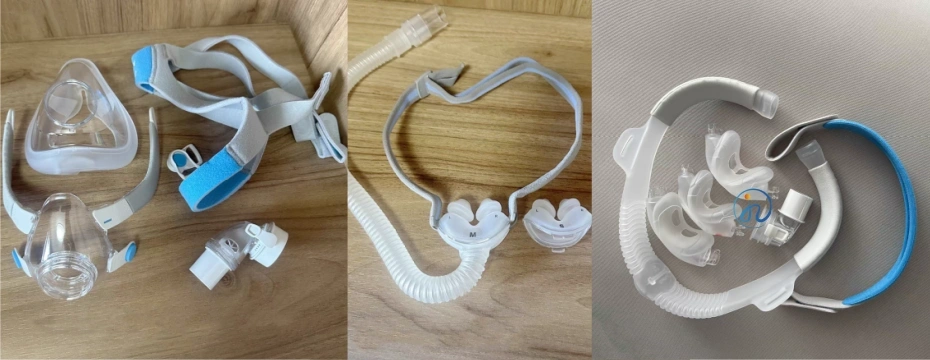
2.2. Sterilization Resistance
Medical products must endure various sterilization processes without degrading. LSR is highly resistant to:
- Autoclaving (steam sterilization)
- Gamma radiation
- Ethylene oxide (EtO) sterilization
This makes LSR products reusable and durable over time—perfect for surgical tools, reusable tubing, and implantable devices.
2.3. Chemical and Thermal Stability
In medical environments, devices may come into contact with bodily fluids, cleaning agents, and temperature changes. LSR can operate from -55°C to +250°C, and its chemical resistance ensures that products maintain integrity under harsh conditions.
This makes LSR suitable for:
- Surgical seals
- Fluid-handling components
- Thermally insulated parts
3. Manufacturing Advantages of LSR for Medical Products
3.1. Precision and Repeatability
With LSR injection molding, manufacturers can achieve tight tolerances and complex shapes, which are essential for precision medical parts. This is crucial for components like:
- Drug delivery system seals
- Microneedle bases
- Valve components
3.2. Clean Room Compatibility
LSR parts can be molded in Class 100 or Class 1000 clean room environments, ensuring minimal contamination. This is a key factor for components used in:
- Implantable devices
- Contact with open wounds or bloodstream
- Diagnostic equipment
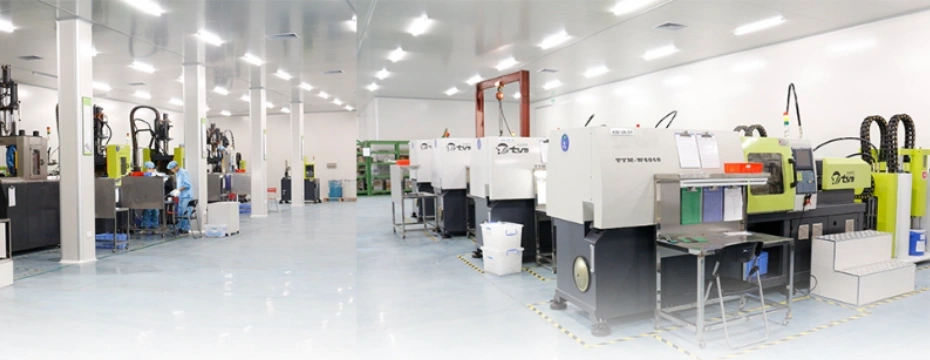
3.3. Automation and Cost Efficiency
LSR injection molding supports full automation, reducing labor costs and enhancing production speed. High-volume production is made feasible without compromising quality.
4. Common Medical Products Made with LSR
Here are typical LSR medical products widely used across healthcare applications:
Product Type | Application |
---|---|
Respirator masks | Anesthesia, CPAP, oxygen therapy |
Tubing and valves | IV sets, catheters, peristaltic pumps |
Sealing gaskets | Diagnostic devices, infusion systems |
Nasal pillows | CPAP and BiPAP systems |
Implanted seals | Long-term drug delivery or orthopedic systems |
Infant care items | Teething toys, pacifiers, baby bottle nipples |
5. Compliance and Regulatory Support
LSR materials used in medical devices are supported by:
- FDA (21 CFR 177.2600) Compliance
- ISO 13485 Manufacturing Standards
- REACH and RoHS Certification
This compliance guarantees the material’s safety and suitability for critical healthcare usage, simplifying regulatory approval processes.
6. Design Flexibility and Patient Comfort
Soft-touch feel and flexibility make LSR an ideal material for devices worn on or inside the body. It conforms to skin without irritation and provides excellent sealing without pressure points.
For instance:
- CPAP masks made with LSR provide a snug fit while maintaining airflow and reducing skin marks.
- Infant pacifiers are soft, non-toxic, and bite-resistant.
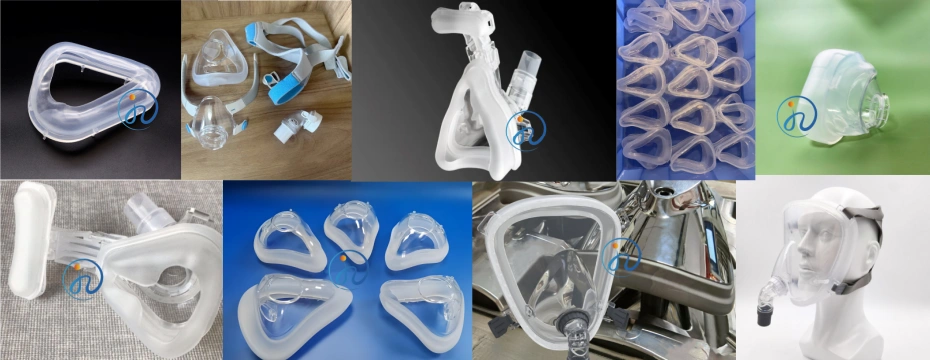
7. Eco-Friendliness and Sustainability
Medical-grade LSR is non-toxic, non-reactive, and recyclable in some applications. Its durability allows for longer product lifespans, reducing waste from disposable alternatives.
8. Future Outlook: LSR in Advanced Medical Technology
As technology advances, LSR is being using in wearable medical devices, soft robotics, and drug delivery systems. Its adaptability to miniaturized and integrated systems makes it essential for:
- Implantable biosensors
- Microfluidic components
- Smart drug delivery patches
Conclusion: Why LSR Medical Products are the Future of Healthcare
LSR’s unique combination of safety, flexibility, precision, and durability makes it the ideal material for modern medical devices. Whether you’re an engineer designing life-saving tools or a buyer sourcing for dependable suppliers, choosing LSR medical products ensures compliance, performance, and patient comfort.
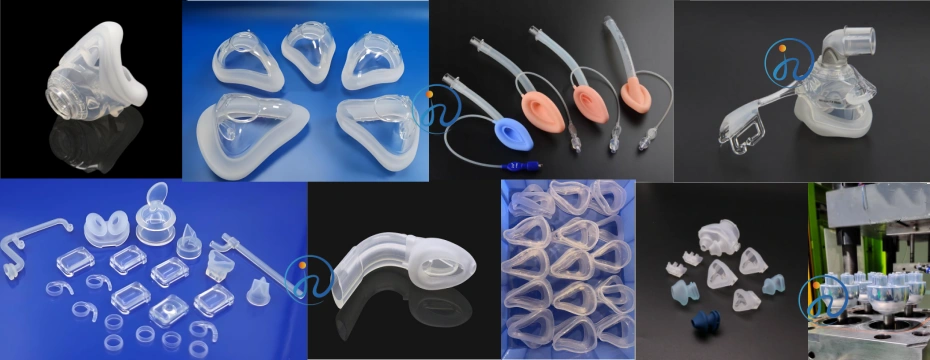
If your project demands reliable and biocompatible solutions, Liquid Silicone Rubber is a smart and future-proof choice.